Spot, the robot dog, on-site at Sellafield. (Photo: AtkinsRéalis)
Sellafield Ltd. and AtkinsRéalis have successfully operated a robotic dog from a remote location in what might be the first time such an operation has happened at a nuclear licensed site, according to the companies in a March 18 press release.
Idaho Cleanup Project crews with the Calcine Disposition Project watch as robotics equipment is tested remotely inside a full-scale replica of a calcine bin set. (Photo: DOE)
A team with the Department of Energy’s Idaho Cleanup Project successfully tested robotic equipment being developed to retrieve radioactive calcine, a granular solid waste, at the Idaho National Laboratory Site, the DOE’s Office of Environmental Management has announced.
SRS liquid waste contractor Savannah River Mission Completion will use drones equipped with cameras to inspect the cleaning status of waste tanks at the site. (Photo: DOE)
The Department of Energy’s Office of Environmental Management will begin using drones for the first time to internally inspect radioactive liquid waste tanks at the department’s Savannah River Site in South Carolina. Inspections were previously done using magnetic wall-crawling robots.
The DOE-EM–Sandia team and Sellafield representatives pose with Spot Robot at the Sellafield Engineering and Maintenance Centre of Excellence. (Photo: DOE)
Robotics experts from Sandia National Laboratories and representatives from the Department of Energy Office of Environmental Management’s Technology Development Office recently visited the Sellafield nuclear site in England to discuss how robotics, artificial intelligence, and other emerging tools can be developed and used in nuclear cleanup operations.
December 2, 2022, 3:03PMNuclear NewsBrian Dassatti, Kamila Blain, and Jenn Sinkiewicz Teledyne FLIR PackBot® conducts visual inspections in a hazardous area.
Mobile unmanned systems, also known as MUS, encompass a range of robotic devices, including drones, ground vehicles, crawlers, and submersibles. They are used for a wide range of industrial and defense applications to automate operations and assist humans or completely remove human workers from hazardous conditions. Robotics are ubiquitous in industrial manufacturing. Military robots are routinely employed in combat support applications, such as reconnaissance, inspection, explosive ordnance disposal, and transportation. Drones are used in many industries for security and monitoring, to conduct aerial inspections or surveys, and to capture digital twins. Wind and solar farms use MUS technologies for day-to-day operations and maintenance.
Nicholas Spivey, left, an SRNL mechanical engineer, and Kurt Gerdes, director of EM’s Office of Technology Development, use virtual reality simulation of an EM worksite during meetings held at the IHMC in Pensacola, Fla. (Photo: DOE)
For the first time since forming in 2020, more than 40 members of a Department of Energy team met in person to evaluate technologies, including exoskeletons and wearable robotic devices, that could be adapted to the cleanup mission of department’s Office of Environmental Management (EM), helping improve the safety and well-being of its workers.
A robot called Lyra was used to survey an underground radioactive ventilation duct in Dounreay’s redundant laboratories. (Photo: NDA)
Dounreay Site Restoration Ltd. (DSRL) and the Robotics and Artificial Intelligence in Nuclear (RAIN) Hub, a consortium of universities led by the University of Manchester, are working together on the development of robots capable of accessing areas that are inaccessible or unsafe for humans to work in. The robots will be used to inspect and characterize Dounreay’s laboratories, buildings, and structures as the United Kingdom prepares to decontaminate and decommission the nuclear site.
Inside the New Safe Confinement covering the sarcophagus of Chernobyl’s Unit 4. (Photo: SSE Chornobyl NPP)
A team of scientists from the United Kingdom’s University of Bristol were given access to the Chernobyl nuclear power plant in Ukraine, advancing a project to train robots and artificial intelligence systems to measure radiation and create 3D maps.
A slideshow of the team’s visit to Chernobyl’s Unit 4 control room and New Safe Confinement structure, where they deployed radiation mapping and scanning sensors, including a LIDAR-equipped robot call Rooster, appears on Gizmodo.
A look at Fukushima Daiichi today. (Photo: The Asahi Shimbun via Getty Images)
News programmers’ hunger for stories about the aftermath of the earthquake and subsequent tsunami that caused three reactor meltdowns at Fukushima Daiichi in March 2011 shows no signs of abating.
The plant’s Program Engineering Department head has overseen significant new technology implementations for maintenance.
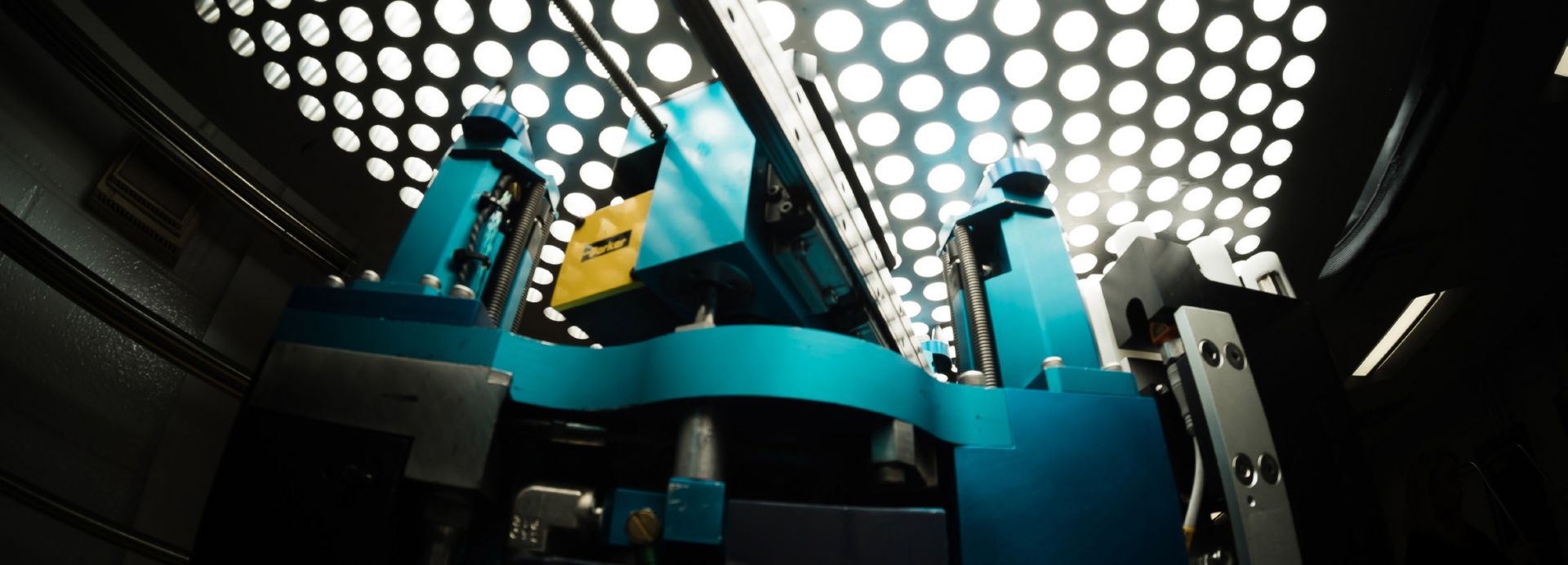
The Zephyr system uses probes for steam generator inspections. Photos: APS
The Palo Verde Nuclear Generating Station, a three-unit pressurized water reactor plant operated by Arizona Public Service Company, has started using an inspection technology relatively new to the nuclear industry. The technology, called smart pigs (an acronym for “piping inline gauges”), has previously been employed by oil and gas companies for inspecting and cleaning underground pipes. After testing and analyzing smart pig products from several companies, Palo Verde’s underground piping consultant, Dan Wittas, selected a smart pig suitable for navigating the tight-radius bends in the plant’s spray pond piping. The spray pond system consists of piping, a pump, and a reservoir where hot water (from the Palo Verde plant) is cooled before reuse by pumping it through spray nozzles into the cooler air. Smart pigs work by using the water’s flow through the piping to move an inspection tool within the pipe itself. The technology replaces the previous method of pipe inspection, in which various relatively small sections of piping were unearthed and directly inspected, and were considered to be representative examples of the overall piping condition. In contrast, the smart pigs obtain corrosion levels for the length of piping traveled through and allow a corrosion baseline to be established.