Remote fuel cleaning from across the globe
In the midst of the COVID-19 pandemic, U.S.-based experts from Dominion Engineering led European workers remotely in the execution of ultrasonic fuel cleaning.
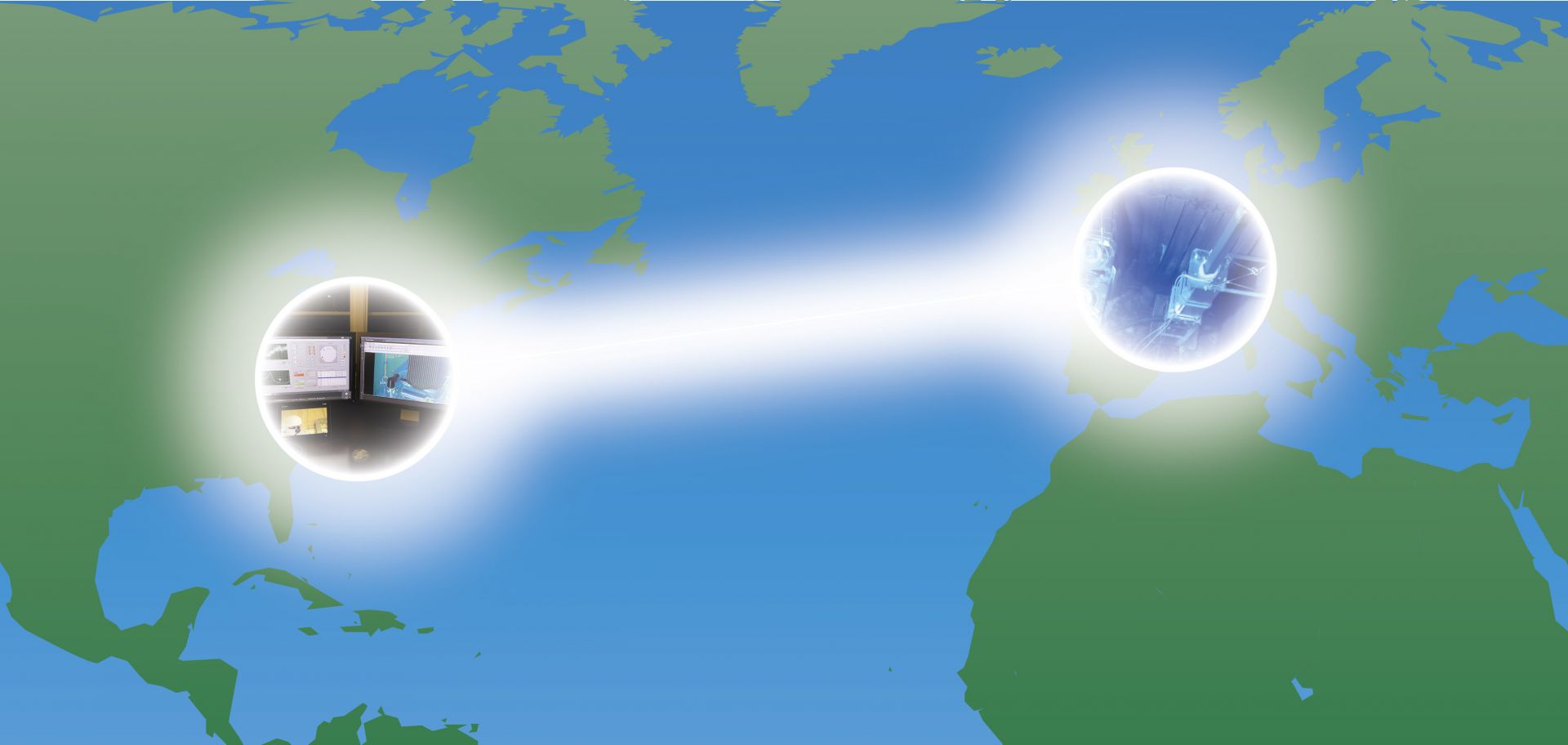
Around the world in the mid-March time frame, conditions were changing rapidly due to the COVID-19 pandemic, as was everyone’s understanding of it. For nuclear power plants, the pandemic meant dealing with new government regulations and restrictions that were put in place. “U.S.-based support of international clients was especially challenging,” said Mike Little, president and principal officer of Reston, Va.–based Dominion Engineering Inc. (DEI). “With border closures going into effect, we were not only focusing on the health and safety of our workers abroad, but also making sure they would be able to return home. Providing remote subject matter expertise from the U.S. through our international service partners was critical to successful job execution during this time.”