Penfield and Enos: Outage planning in the COVID-19 era
Regulatory relief, remote working, sanitation, and communication were key factors in the success of the spring refueling outage at Beaver Valley-2.

Penfield
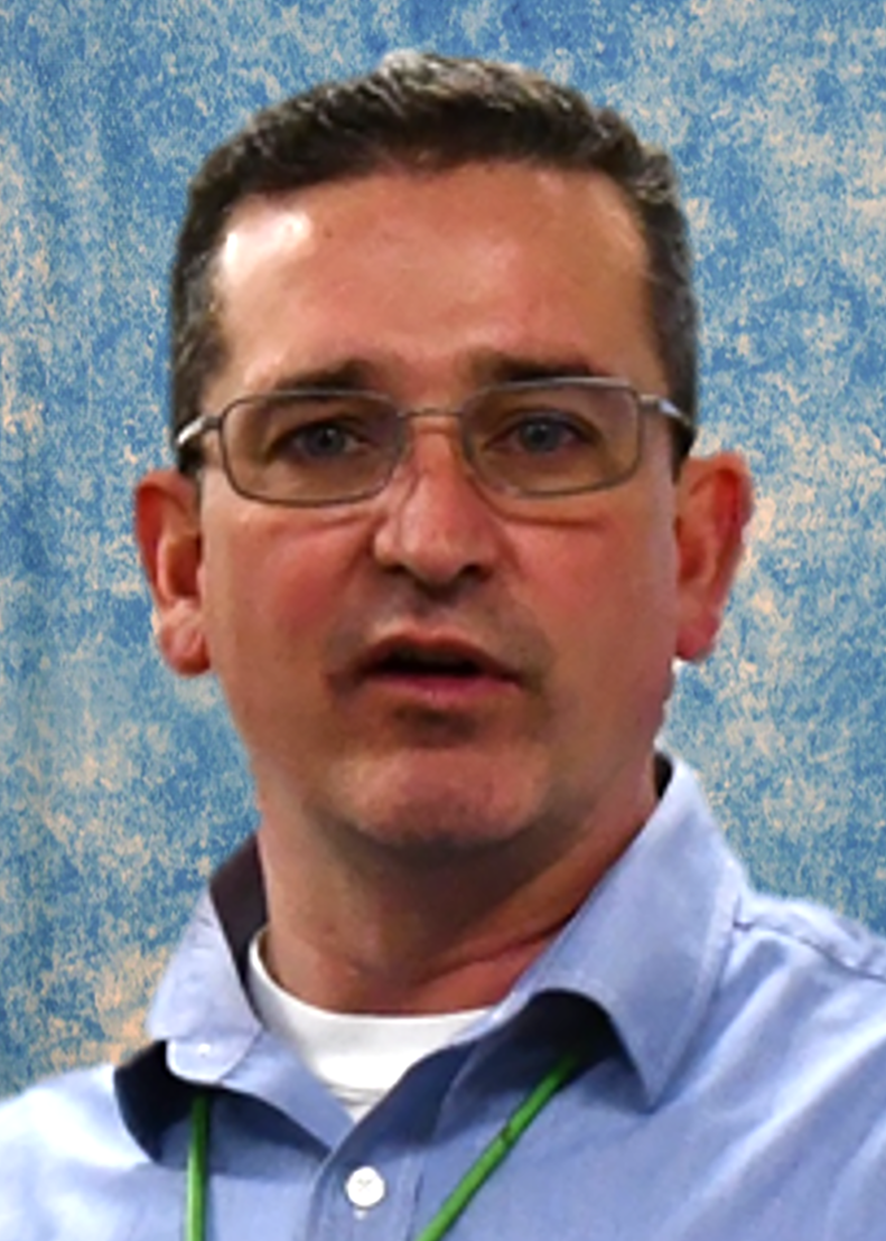
Enos
Energy Harbor’s Beaver Valley plant, located about 34 miles northwest of Pittsburgh, Pa., was one of many nuclear sites preparing for a scheduled outage as the coronavirus pandemic intensified in March. The baseline objective of any planned outage—to complete refueling on time and get back to producing power—was complicated by the need to prevent the transmission of COVID-19.
While over 200 of the plant’s 850 staff members worked from home to support the outage, about 800 contractors were brought in for jobs that could only be done on-site. Nuclear News Staff Writer Susan Gallier talked with Beaver Valley Site Vice President Rod Penfield and General Plant Manager Matt Enos about the planning and communication required.
Beaver Valley can look forward to several more outages in the future, now that plans to shut down the two Westinghouse pressurized water reactors, each rated at about 960 MWe, were reversed in March. “The deactivation announcement happened in the middle of all our planning,” Enos said. “It’s a shame we haven’t had a chance to get together as a large group and celebrate that yet.”
While the focus remains on safe pandemic operations, the site now has two causes for celebration: an outage success and a long future ahead.