Insights from the Three Mile Island accident—Part 1: The accident
Sparked by an article on the TMI accident that appeared in the March 2019 issue of Nuclear News, ANS past president William E. Burchill (2008–2009) offered his own views on the subject. Part 1 of the article appeared in the May 2019 issue of NN and Part 2 was published in June 2019.
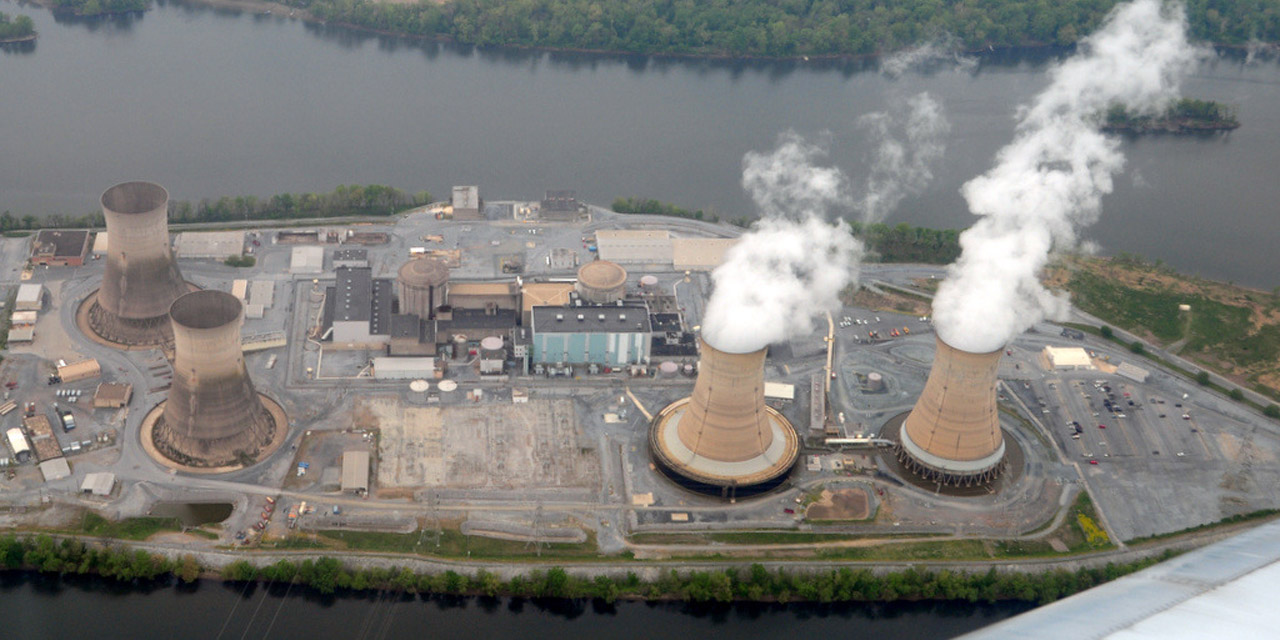
The accident at Unit 2 of the Three Mile Island nuclear power plant on March 28, 1979, was an extremely complex event. It was produced by numerous preexisting plant conditions, many systemic issues in the industry and the Nuclear Regulatory Commission, unanticipated operator actions, previously unrecognized thermal-hydraulic phenomena in the reactor coolant system (RCS), and the unprecedented challenge of managing a severely degraded core.