ITER updates: Components, commitments converge toward first plasma
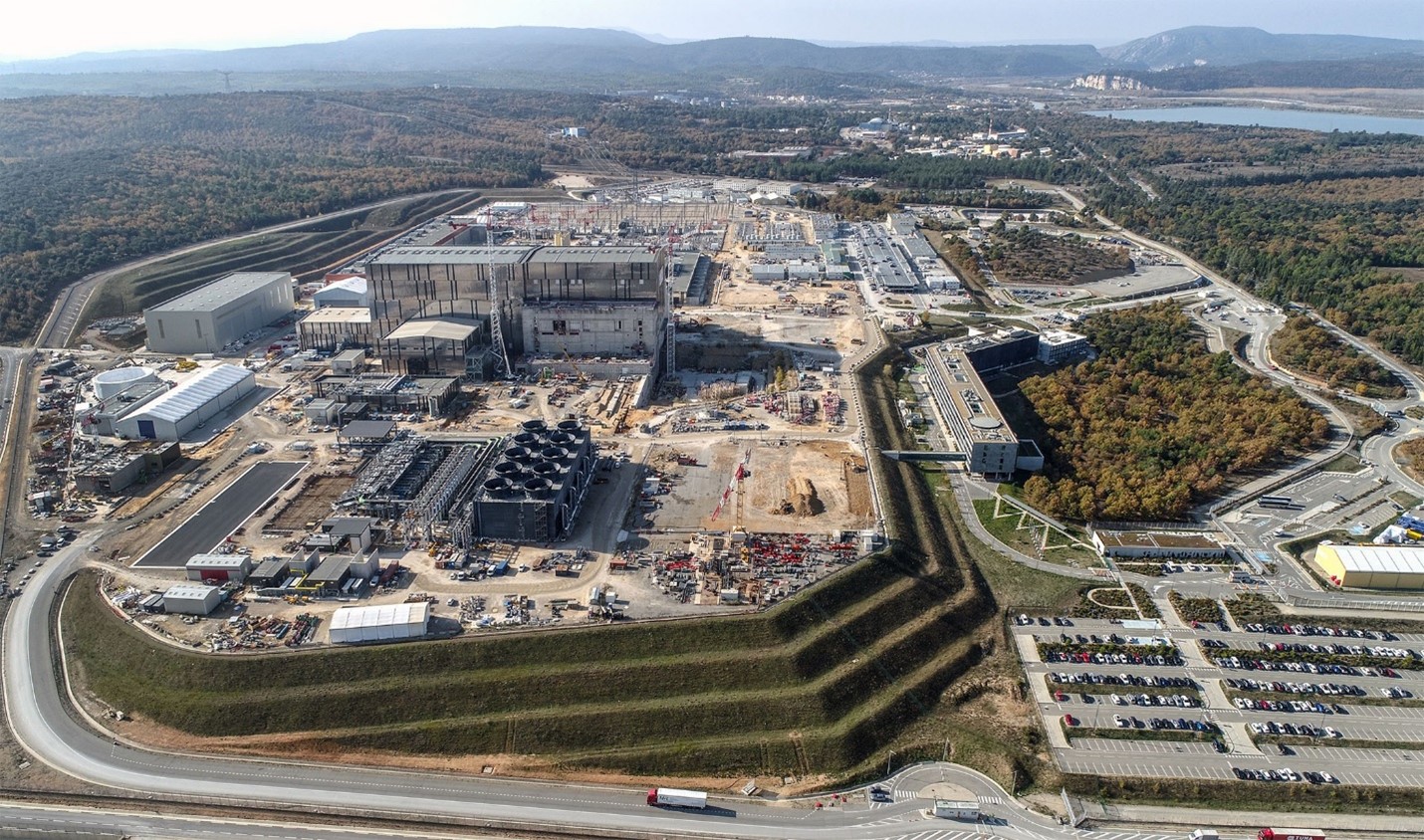
The ITER site in Cadarache, France. Photo: ITER Organization
With first plasma operations at ITER planned for 2025, milestones are being reached in quick succession. While several of the 35 countries contributing to the construction of the super-sized fusion tokamak are pursuing fusion programs of their own, they remain committed to ITER and are eager for the data and operating experience it is expected to yield.
Euratom leads the project being built in Cadarache, France, as the host party for ITER. On February 22, the European Council approved the continuation of European financing of ITER from 2021 to 2027, with a contribution of €5.61 billion (about $6.86 billion) in current prices.