Arresting debris-related fuel failures
by Mike Little and Dale Vines, Dominion Engineering, Inc.
Now how did that get there?
Finding foreign material in your reactor system is not the beginning of a good day. Where did it come from? Did someone leave this in here or did something break? When did this happen? These are all good questions for which we need to know the answers.
And why do we need to know the answers? It’s all about the fuel. INPO recently released INPO Event Report IER L2-19-6, Preventing Debris-Induced Fuel Failures, which is a means to address the rise over the last five years in fuel failures at nuclear power plants. After a period of very targeted focus to reduce the number of “leakers”, the commercial nuclear industry is now seeing an uptick in fuel leaks, which is not helping our industry drive toward better and more cost-effective operations. It is estimated that each fuel failure can cost a utility several million USD or more due to plant downtime, increased regulatory scrutiny, and restoration-related costs.
So why are we seeing this negative trend in performance? Foreign material is a common cause of fuel failures, particularly at BWRs. While many of us have focused on FME prevention from reactor service activities—mainly because we have beat that drum consistently over the last 30 years—that alone may not be the culprit. More and more we are seeing that long term component degradation and failure to retrieve objects from many years past play an important role in contributing to fuel leaks. As our plants age, common modes of failure such as deteriorating valve seats introduce material that can be transported throughout our reactor system and ultimately end up affecting fuel reliability. And if it can get there it will, no matter how unlikely it may seem. This type of material is not only a concern to fuel integrity; foreign material containing StelliteTM may become activated, and significantly elevate Co-60 levels in reactor water and thereby increase plant dose rates.
Step One: Getting It Out
This material can sometimes become trapped on the underside of lower tie plates in fuel assembly bottom nozzles as it migrates through the reactor system, and this provides an opportunity to remove foreign material before it breaks into smaller fragments and migrates past the lower tie plate into the fuel bundles. However, removing foreign material can be labor intensive and time consuming, making it challenging and expensive to remove foreign material from large numbers of fuel assemblies– especially as refueling outages become shorter and shorter.
One method that has proven successful at several nuclear plants is using ultrasonic cleaning systems. Dominion Engineering, Inc., has developed several equipment systems which utilize a combination of ultrasonic energy and reverse flow to disrupt and capture foreign material. Our Bottom Nozzle Cleaning (BNC) system is used for cleaning and inspecting the bottom nozzle of a
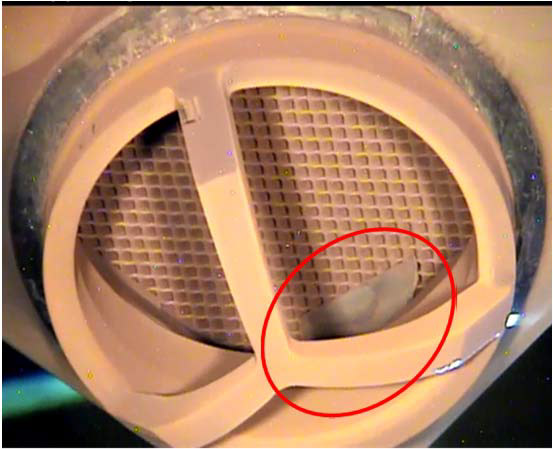
Before
fuel assembly, while our High Efficiency Ultrasonic Fuel Cleaning (HE-UFC) system is used to remove crud and debris from the full length of the fuel bundle including the bottom nozzle assembly. Our cleaning systems are designed for quick and efficient removal of foreign material from fuel assemblies, and simultaneous inspection to confirm foreign material removal – making it practical to efficiently complete this process on large numbers of reload fuel bundles during refueling outages.
As you can see from the pictures, material that is trapped on the underside can
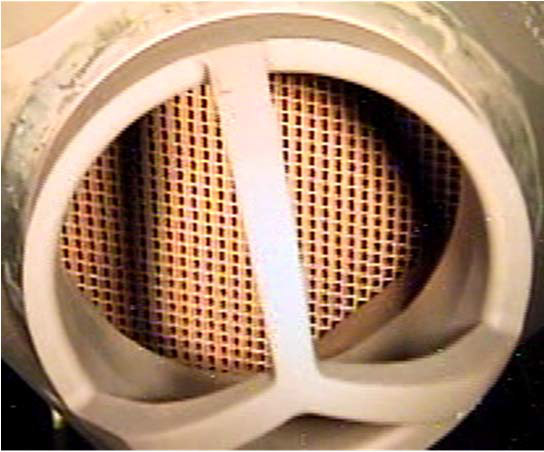
After
stay attached to the tie plate even during fuel movement activities.
This is a tricky situation; unless each assembly is fully inspected during the reload, the material can remain multiple cycles, vibrating and continuing to release small fragments that can now enter the fuel bundle and potentially cause damage. Once the fuel assembly is inserted into the ultrasonic cleaning system, the ultrasonic process breaks the material free from the tie plate, thus allowing it to be removed from the fuel system and subsequently captured for further analysis. An added benefit to using this system is that cleaning, inspection, and capture can occur in parallel during the ~ 2 minute process required to complete each assembly.
Impressive results have been achieved using ultrasonic cleaning systems. They have been helpful in arresting fuel failures at units experiencing persistent debris-related fuel failures as well as removing up to several pounds of foreign material and >100,000 Ci of activated foreign material at a single unit.
Step Two: Identifying the Source
Once the material is removed, it becomes very important for us to understand where it came from and identify what we can do to either remove or mitigate future introduction of this unwanted source of foreign material. While our ultrasonic cleaning systems allow for easy collection of material retrieved from the fuel assembly’s bottom tie plate, there are other locations and methods of removing unwanted objects. No matter which method you use, the critical action is to now determine what it is and where it came from.
As discussed in IER L2-19-6, Recommendation 2.c, characterization of the debris is necessary to identify the source. Technology has come a long way in the past two decades, and plants now have many cost-efficient options to properly and accurately determine the material’s origin. These include visual inspection, offsite laboratory evaluation, and onsite material composition analysis. If you can determine the composition or source either visually or analytically, differentiating characteristics of components (composition, age/vintage, etc.) may be used to determine which ones may be introducing the material. Sometimes you may already be aware of the source; i.e. a component degradation or foreign object intrusion that occurred years if not decades ago…the material can take a good amount of time to make its way into the vessel. And in some cases, it may be a new or developing situation that requires action to prevent additional material generation. Whatever the case, proper classification and understanding is the key to long-term fuel health.
DTE’s Joe Ferguson, Radiation Protection ALARA Manager at Fermi, is looking forward to his next spring’s outage to tackle this challenge head on:
“Fermi has experienced several debris ingress and crud release events that have led to fuel failures and higher dose rates in plant piping. Even prior to the issuance of INPO IER L2-19-6, we had proactively decided to perform ultrasonic cleaning of the fuel during the upcoming refueling outage in order to mitigate debris-related fuel failures in addition to reducing the effects of any future crud release events. To better understand the root cause of previous fuel failures, we will also be performing ultrasonic cleaning of discharge fuel bundles from prior cycles with known fuel failures to collect and characterize potential debris sources from those bundles. This has very much been a collaborative effort between Reactor Engineering and the Radiation Protection department which we expect to provide long-term benefits to our site.”
Step Three: Eliminating Future Fuel Challenges
Once the source is identified, you are not quite done. Depending on what the material is and where it came from, a detailed remediation plan may be required. Repairing and/or replacement of a deteriorating component is paramount, but you also must determine if any other pieces may have been released and not yet recovered. The use of system transport models is one method to identify the areas that may hold similar objects that have not made their way to the reactor vessel and to develop flushing or inspection protocols that could remove any remaining foreign material. Of course, these plans need to be evaluated based on a systematic approach to the potential risk versus the perceived gains from early removal. There may be more benefit to creating a robust monitoring plan instead of attempting an arduous removal plan that may not yield definitive results.
DEI is committed to helping the nuclear industry arrest fuel failures and eliminate debris-induced challenges going forward. In addition to our ultrasonic cleaning activities, we have introduced several filtration and inspection products that can help locate, remove, and collect foreign material from the reactor system. Reach out to us today to discover how we can help with your response to IER L2-19-6.
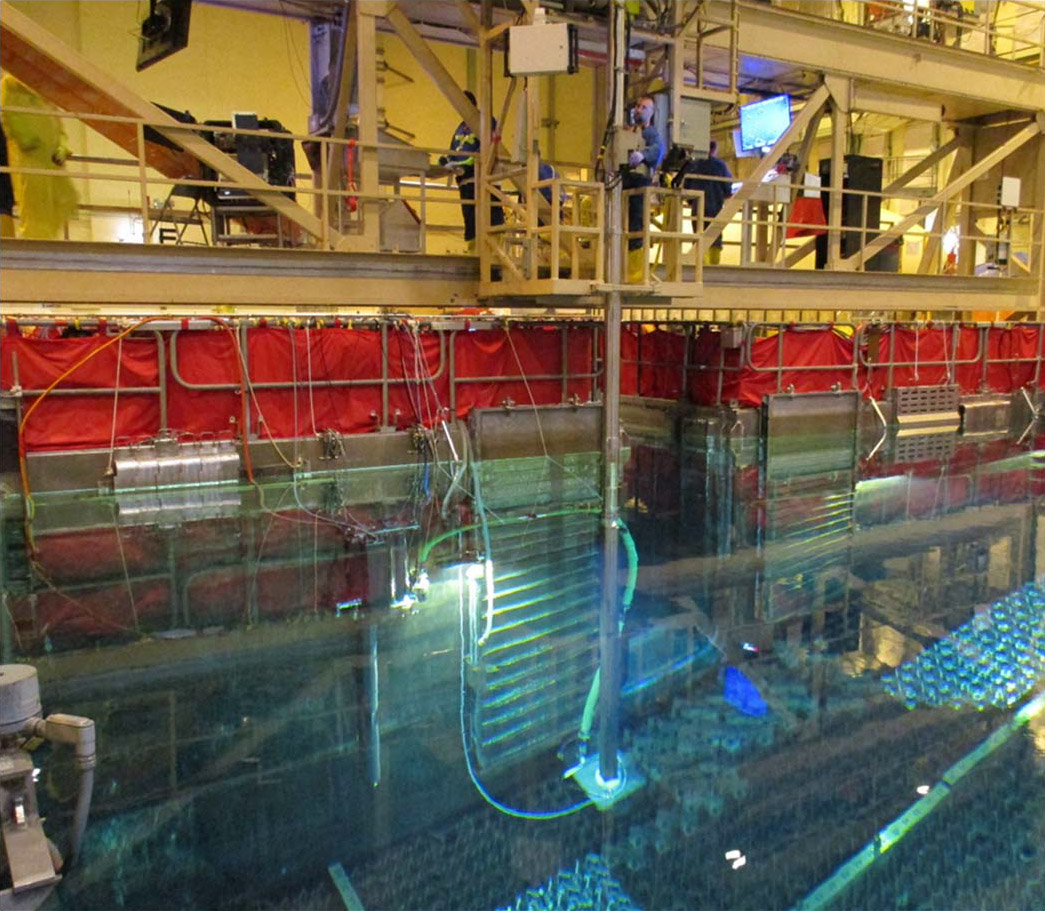
BNC System Installation
For more information, contact Dale Vines (dvines@domeng.com) or Mike Little (mlittle@domeng.com), if you have questions or would like to discuss options for reducing debris-induced fuel failures.