Modernization of the existing fleet: Gaining speed!
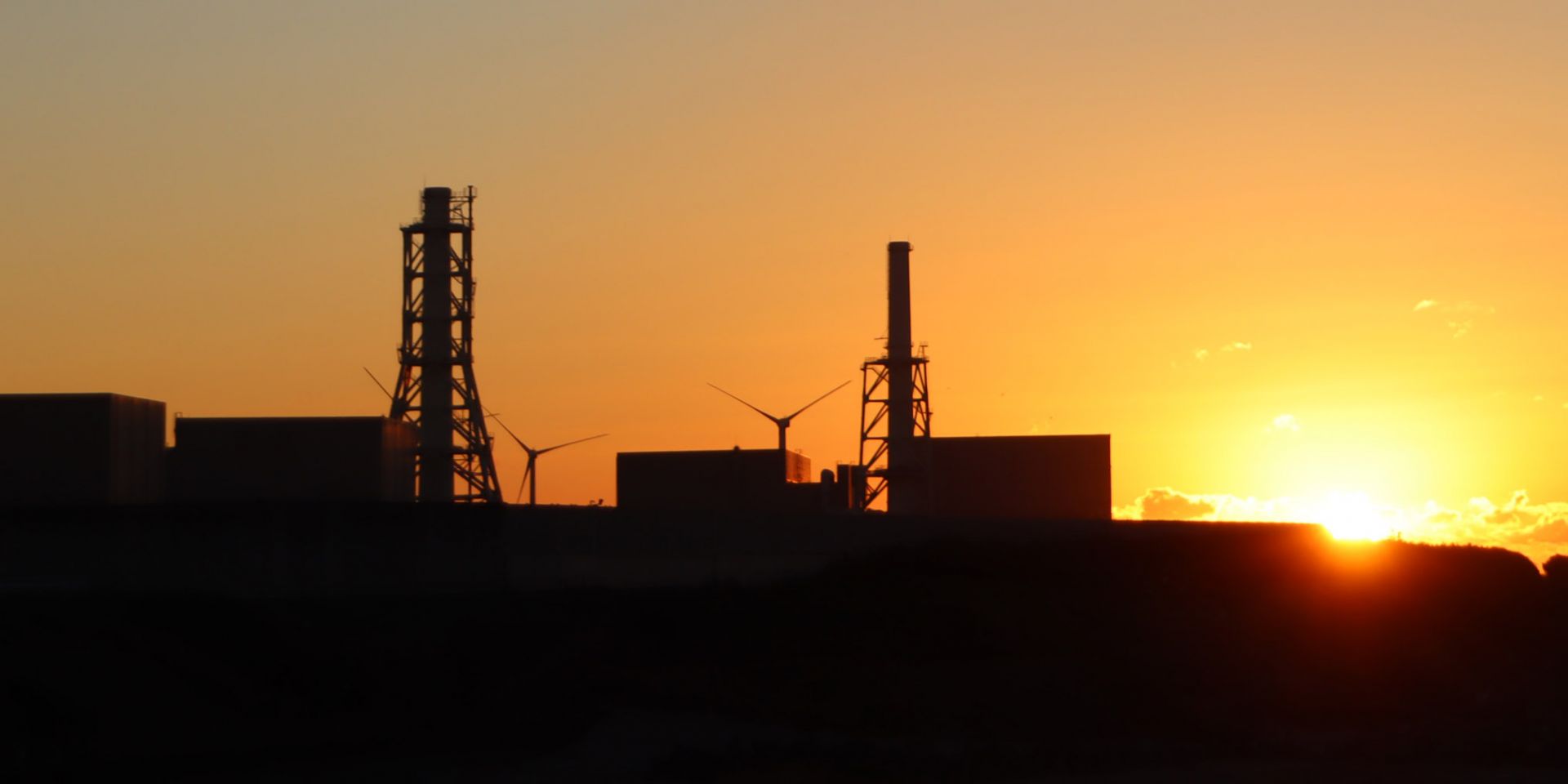
“It is critical after the Hamaoka Nuclear Power Station restart that we reduce our cost and increase our capacity factor while becoming more economically competitive.” Ichiro Ihara, chief nuclear officer of Chubu Electric Power, made this observation recently when the Electric Power Research Institute visited the Japanese nuclear power plant for a strategy development session for plant modernization. EPRI’s team of five specialists spent four days at Hamaoka to investigate the feasibility of potential improvements—the third step of the EPRI modernization strategy planning process. It was a trip six months in the making—and the first time EPRI has applied its nuclear plant modernization process outside the United States.