Second waste retrieval machine installed at Sellafield
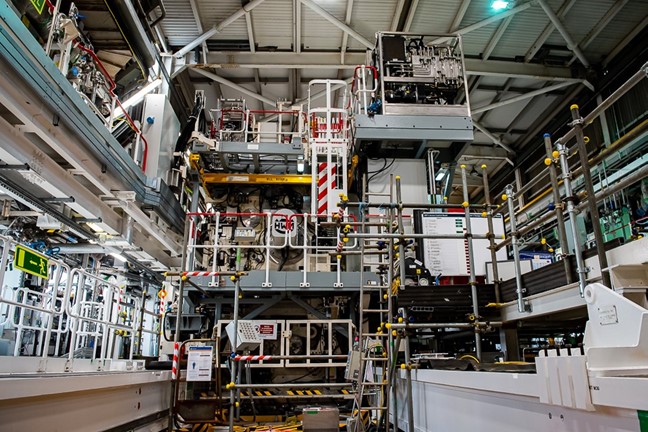
The second of three machines that will be used to safely remove waste from the Magnox Swarf Storage Silo at the Sellafield nuclear site in the United Kingdom has successfully been assembled, it was announced by Sellafield Ltd., a subsidiary of the U.K. government’s Nuclear Decommissioning Authority.
A video showing how waste is removed and the Magnox Swarf Storage Silo prepared for decommissioning has been posted to YouTube and can be found here.