Delivering Massive Efficiency (and Bottom-Line) Gains Through Chemical Descaling
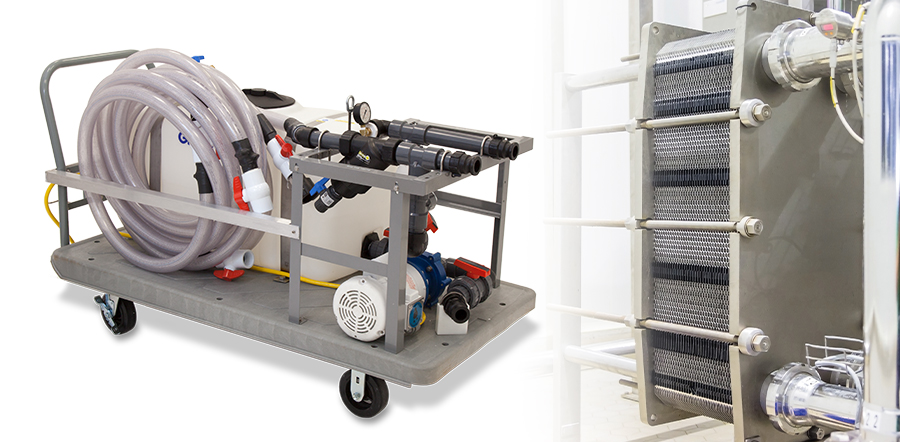
Power generation has many factors and key indicators to identify the “health” of a plant. Some macro-level indicators are vital to help identify challenges before they become problems; others are less sensitive yet just as important. Micro indicators such as condenser return temps or changes in pump pressures can be critical indicators of a problem that few understand, yet which results in enormous loss of efficiency. That problem is deposits on critical system tubing and piping caused by calcium carbonate or other mineral buildups. The bottom line? Scaling is a significant issue in power plants that can considerably impact efficiency and profitability.
Part of the challenge with scale buildup is the water source. Most power plants use water sources near them, generally, rivers, lakes, or other raw water sources, while others have built cooling water lakes, or ponds, often from soft limestone rock formations. The most common use of this water is in single-pass operations, which run through a plant’s critical system, do the cooling job, and then return to the source or other storage areas.
This approach’s benefit is easy access to significant water sources that can help cool critical machinery. The disadvantage, however, is due to the single-pass nature of the raw water, water treatment is not a realistic approach, and this water tends to have a high mineral content, which, when used in the heat exchange process, increases the accumulations of scale.
So, how much impact does scale buildup have on a power plant?
In a recent job that Goodway was included in, a nuclear power plant had a substantial decrease in megawatt production due to scale accumulations within their condenser tubes. Their initial plan was to use mechanical cleaning with scraping projectiles. Scrapers were at a point of getting stuck during cleanings and the plant knew they had to reset the condenser clock. And we know the golden rule. Efficiency = profitability. Through careful planning, we were able to help the plant achieve a successful cleaning by coaching their contracted service group through the entire process. The cleaning resulted in a return of 6-8 megawatts. Goodway worked with another nuclear power plant to clean their containment spray heat exchangers. The pressures went from 69 to 9. The plant was so impressed the second unit was scheduled.
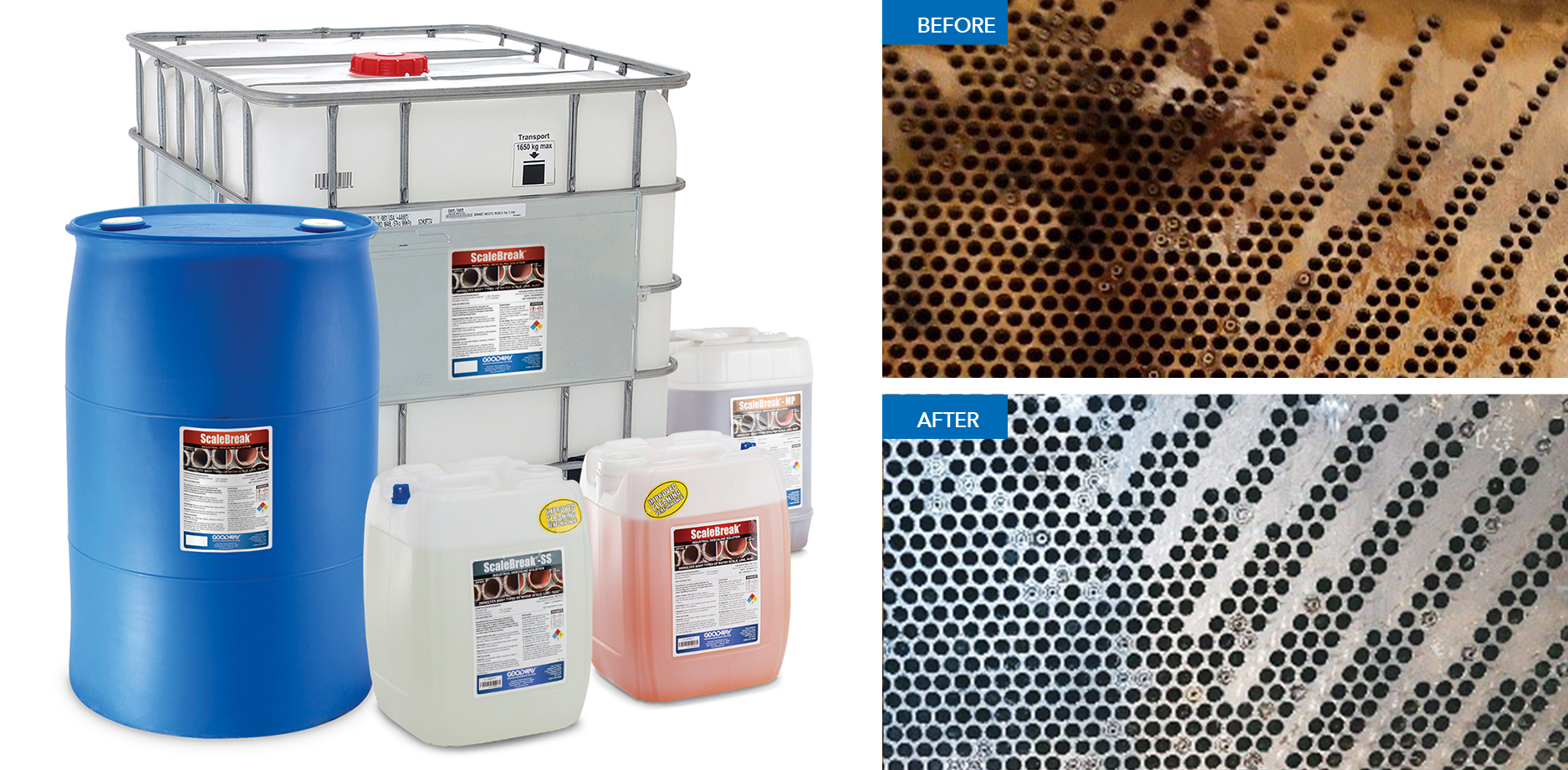
Goodway Technologies ScaleBreak®
Critical systems like condensers, which are generally cooled by this raw water, quickly lose efficiency due to scale buildup. Loss of efficiency equals loss of megawatts. The primary effect of this efficiency loss correlates directly to the plant’s profitability and ability to supply contracted amounts of power. Additionally, the increased scale buildup requires systems to work longer and harder, leading to premature failure and expensive downtime. Preventive maintenance in a timely, effective manner becomes imperative. Preventive maintenance programs ensure efficiencies remain intact, reducing production cost increases and prolonging capital equipment investments.
While tackling preventative maintenance can be part of the ongoing balance of plant activities for smaller heat exchangers or other systems, larger condensers and production critical equipment requires pre-planning. Proper identification of the makeup and thickness of scale in the system, planning, and resource allocation is paramount to a successful cleaning. Power plant units are on tightly preplanned outage schedules. Plants know when they are losing efficiencies, so returning a condenser to efficient operation within the scheduled outage timeline is imperative. If a unit requires an extended outage outside of the pre-planned expectations, this can affect the planning schedules of other unit outages so the plant can meet its contracted power supply. Recent history supports this where a potential plant, because another outage ran over schedule, could not extend any other outage timeframes and still meet their contracted power output. Their condenser remains scaled, and their megawatt production has decreased.
Many plant outages occur in the spring and fall months when power demands are lessened, which proper pre-planning of the outage timeline allows for identifying and contracting those resources. Coordinating all the equipment requiring maintenance and executing the cleanings is a careful orchestration of hundreds of contractors.
Having the correct solutions to potential problems becomes imperative to maintaining scheduled timelines. Solutions for removing scale can sometimes be oversimplified. Many different mechanical solutions can physically remove scale from tube walls and some piping. But can be limited when scale appears in source piping. Technologies like high-water pressure jetting and shooting projectiles can be reasonable solutions in some limited situations. However, descaling with acidic chemicals tends to have the best impact, with the least amount of manual labor and risk for damage. High-performance solutions like ScaleBreak, from Goodway Technologies are fast-acting, biodegradable, and available in various formulas to meet each customer’s needs and their systems’ underlying alloys.
Choosing the right descaling solutions is vital to maintaining the plants’ safety and reducing any harmful effects of chemicals used. Critical decisions about the chemical makeup, the wetting and penetrating agents included, and the types of acids used must be considered. Goodway Technologies has provided descaling chemicals for many power production facilities, including nuclear. Our descaling experts work hand-in-hand with plant engineers, chemists, and regulatory professionals to identify the correct formula and volumes needed.