Ultra Safe Nuclear and ORNL strengthen bonds with 3D printing technology
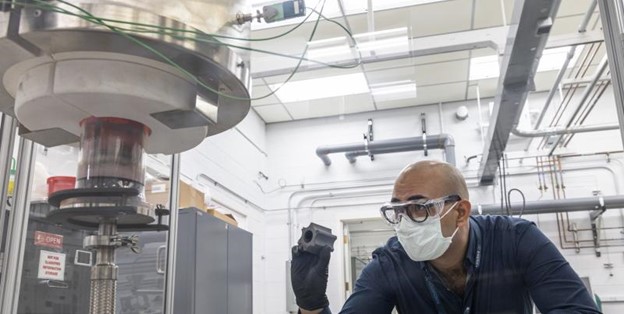
Ultra Safe Nuclear Corporation (USNC), a Seattle-based reactor developer, has licensed an additive manufacturing technique developed at the Department of Energy’s Oak Ridge National Laboratory to print refractory materials into structural and core components for the company’s microreactor designs.