SNUPPS - Nuclear Plant Construction at the Cutting Edge, 1972
Nuclear plant construction became mired during the latter half of the first big nuclear build in the 1970s in a morass of schedule delay and cost overruns, at that time for a variety of reasons-some societal, some regulatory, some economic, and some intrinsic to the overall process. One group of utilities, though, found a way to streamline some of the processes required to get such enormous projects engineered, ordered, and built-and did so without sacrificing quality or safety. The name of the project was SNUPPS, an acronym for Standardized Nuclear Unit Power Plant System, and it may be that some of the lessons learned in that earlier era could well be reapplied (and relearned) today.
Nuclear plant ordering and construction in the early days
Of course, the utilities that wished to buy and operate nuclear plants in those days faced a complex set of requirements (and contracting options) in order to get the job done. Some early nuclear plants were known as "turnkey" projects-the supplier of the reactor would arrange contractually itself for construction of the entire power plant at a fixed cost to the buyer. Other early plants had significant government input (such as the U.S. Atomic Energy Commission [AEC] ownership of the reactor and/or waiver for fuel costs for several years.) However, by and large, the construction of early nuclear plants required the prospective owner-operator (an electric utility company) to contract for detailed design of the nuclear plant (with an architect-engineer firm), the construction of the nuclear plant (with one or more construction contractors), the supply of the nuclear steam supply system or NSSS (with a reactor vendor), and turbine generator or TG (again with a vendor) and supply for the balance of plant and many various other pieces of equipment with further contracts. Management of all these various forces, and all of their innumerable sub-contractors (and thousands of workers in many locations), could get complicated and messy-and could lead to delays, problems, failures, and lawsuits. In many cases, some or all of these happened. (Only a few utilities, such as TVA, Duke Energy, and Detroit Edison, had the ability to perform major portions of this work entirely in-house.)
Some architect-engineer firms (A-E in industry speak) had the resources to not only design but actually provide construction management for the nuclear plants; these included Bechtel Corporation, EBASCO Services, United Engineers & Constructors, and Stone & Webster, among others. This reduced the number of firms the utility had to interface with and attempt to manage.
It must also be remembered that during the early years of nuclear plant construction, the designs of major pieces of equipment-the NSSS or "primary plant" foremost-were not standardized, but rather were in a continual state of evolution to both improve performance per dollar of cost, as well as to drive up output. This was thought to be required to meet the competitive situation between major reactor vendors and to help with the economy of scale relationship that was showing at that time that small units were less economical to build and operate. In 1972, the AEC formally asked all parties to halt growth of nuclear plant output (at 1300 MWe, which roughly correlates to reactors in the 4000+ MWt range) and to standardize the designs of the NSSS with the implicit promise that licensing could begin to move from an individualized approach (design by design AND location by location) to something more streamlined and workable. Of course, the eventual result was the Design Certification process we have today. That was not yet available in the early 1970s-a time when not even standardization seemed like the obvious solution to everyone.
The AEC suggested that the ultimate option (among several offered) to speed up licensing was the process of duplication-wherein identical nuclear plants ("power blocks," or combinations of reactor building, turbine building, and adjoining structures) were built in multiple locations. Only Byron and Braidwood nuclear plants were full duplicates of each other built by one utility, although such A-Es as Bechtel and Stone & Webster did have "reference designs" that were used as basic starting points for nuclear plants ordered by various customers. These designs were only changed incrementally between projects for different customers, and of course were modified for optional equipment and site specific needs. In the case of Stone & Webster, the design lineage first used at the Maine Yankee plant was repeated closely at the Surry plant, then at the North Anna plant, then at the Beaver Valley plant; Millstone Unit 3 was also similar to North Anna's two units. Teams moved from one site to the next and became increasingly valuable as experience was gained. Construction leads moved from Unit 1 of a two-unit site to Unit 1 of the next two-unit site, typically. In addition, Stone & Webster in a pioneering effort toward standardization developed fractional network plans ("Fragnets"), which covered parts of systems or whole systems, standardized for pressurized water reactor or boiling water reactor plants and which included design, engineering, and procurement. Subsequent fragnets included construction, pre-operation checkout, and turnover to the owner. These were unique to Stone & Webster, and were intended to speed up schedules and lower costs. Hundreds of these system and subsystem fragnets were built for PWR and BWR plants.
The industry had already begun, then, in the 1970s to respond to the delays being caused by the vast amount of work required to get the huge number of nuclear plants on order designed and built.
SNUPPS Is born
It was in that environment of change that an executive of Northern States Power Company (NSP), which had bought the wholly unsuccessful Pathfinder Atomic Power Plant (which is a whole story unto itself) and was in the process of buying two completely different types of nuclear plants, proposed in 1972 a rather innovative management approach. At an industry meeting in Chicago, Wade Larkin of NSP proposed to both industry executives and nuclear vendors an idea that was quickly termed "SNUPPS"-or Standardized Nuclear Unit Power Plant Syndicate-wherein a syndicate of utilities would solicit bids from vendors on nuclear plant contracts and equipment with the basic notion that the volume order could reduce the cost to each utility for multiple reasons. Twelve utility companies were originally involved in the plan; probably correctly, the acronym was soon restyled to "Standardized Nuclear Unit Power Plant System" to remove any negative connotation of the word "syndicate."
By late 1972 only five utility companies remained in the group: Kansas City Power & Light, Kansas Gas & Electric, Northern States Power, Rochester Gas & Electric, and Union Electric Company. These companies decided upon a radical and unique plan to order a group of perfectly identical nuclear power plant power blocks (reactor containment building, turbine generator building, and adjoining support buildings) for all of the utilities for the group.
SNUPPS becomes reality
The unique project management scheme for SNUPPS was the formation of Nuclear Projects, Inc. (NPI) by the participating utilities to manage the (identical) contracts signed between the utilities, the vendors, and the A-Es. Bidding was accepted for major plant components (NSSS, TG) and for the contract to act as A-E on the basis that vendors would only charge once for the usual engineering costs, which would be split between the participating utilities. In 1973, Westinghouse was awarded the NSSS contract, GE the TG contract, and Bechtel Corporation the A-E contract. Each provided equipment or services to the group, with basic or one-off engineering (not equipment cost) charges normally charged per each nuclear plant ordered instead charged just once and spread among the whole. NPI presented a single, unified face to both the industry and, interestingly, to the U.S. Nuclear Regulatory Commission, which decided that because of the perfectly identical design of all the nuclear plants being built under SNUPPS, it would assign lead responsibility to a team in its Region I for all the units spread over three NRC regions. (The power blocks were identical even down to the color of the aluminum siding.)
Originally, six power blocks were ordered: two-unit plants were to have been Callaway (Missouri, Union Electric) and Tyrone (Wisconsin, NSP) while single-unit plants were to have been Wolf Creek (Kansas, KG&E/KCP&L) and Sterling (New York, RG&E). Tyrone Unit 2 was almost immediately cancelled. The two-unit sites had power blocks that shared no systems between blocks, making them identical to those on any other (single-unit) site.
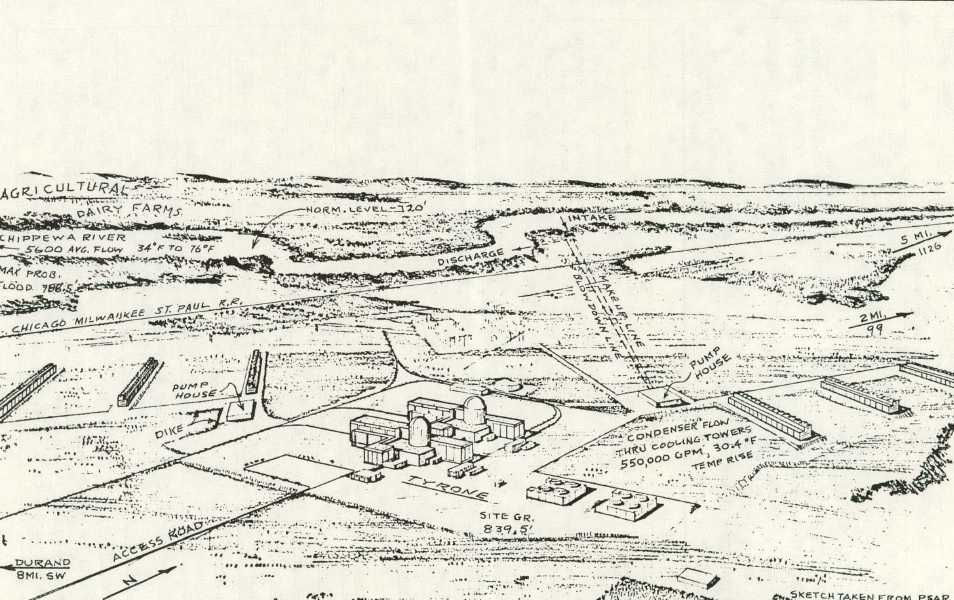
Northern States Power's Tyrone Energy Park as originally envisioned. Both units were eventually cancelled. Illustration from ORNL-NSIC-55 Vol. IV, "Design Data and Safety Features of Commercial Nuclear Power Plants." Illustration originally from PSAR for Tyrone and modified for this publication.
Savings under the agreed structure were to be many. The effort to perfectly duplicate the power blocks at all these units drove up design cost for the A-E; however, engineering cost for each of the units was only 40 percent that of normal. Spare parts cost would be reduced by sharing parts between units. Training of operators would be shared between SNUPPS units, reducing this cost to owners. Centralized record-keeping would further reduce administrative costs. Shortening the licensing process by having only one set of hearings for radiological safety aspects of all units was also facilitated, with the NRC's cooperation. Total savings, according to Nuclear Engineering International (September 1977) were expected to be 10 percent per unit of the plant costs, or else $100 million on a roughly $1 billion nuclear power plant.
What actually happened
The history of the SNUPPS units didn't quite pan out as originally intended although this wasn't the fault of duplication or the management scheme. Caught up in the general downturn of projected power demand in the country in the late 1970s and early 1980s, and faced with increasing inflation and capital costs, all units other than Wolf Creek and Callaway Unit 1 were eventually cancelled. Although the plan originally had been to get construction permits for the early plants within one year to one-and-a-half years after submitting Preliminary Safety Analysis Reports, the general slowdowns of licensing (including a moratorium for a time in 1976) greatly delayed the process. In 1985, Wolf Creek was estimated to cost $2.9 billion (instead of $1 billion) but it was reported (Nuclear Engineering International, July 1985) that cost savings from standardization were some $214 million. Callaway Unit 1 entered commercial service in December 1984 while Wolf Creek entered commercial service in September 1985. (Originally intended commercial operation dates for these units were October 1981 and April 1982, respectively, making both units roughly three years late.) The two units took roughly 11-12 years from NSSS and TG order to commercial operation.
One of the most significant challenges to the entire standardization process was actually regulatory; the NRC did not standardize its licensing, particularly on seismic issues. Regulators employed an incremental improvement process as the foundation of their regulatory approach; in this concept, if any nuclear plant "learns a lesson," that lesson must be employed (read as "retrofitted") at all nuclear plants under construction in order for that lesson to have been considered "learned."
Also, regulators could not seem to determine whether or not some nuclear plant components should be fixed solidly or allowed to be flexible (relative to their ability to withstand seismic input). This indecision led to changes in how equipment was placed, the number and location of embedments and pipe hangers, and the strength of materials. Detailed engineering for systems (required to construct them) was changed several times at various plants as the regulator gained knowledge, changed guidance, and then forced redesigns and construction changes-even for completed work, and for nuclear plants nearing completion.
Other challenges to standardization generally (if not duplication) were site limitations (such as at North Anna, where there was no barge access and limited rail access, which limited the size of components or component parts that could be delivered) and owner preferences (where, for example, utilities wished to specify particular types of equipment to match with equipment already in use at other plants built previously). In these ways, "standard plants" became somewhat less standardized.
All that said, the industry and the NRC did work together through all of these issues to develop the regulatory process of today (the "three part" process consisting of design certification, site permit, and combined construction and operating license), which has enabled the "next generation" nuclear plant construction we are now seeing to occur. In that sense, the drive toward standardization in the late 60s and early 70s-which truly was spearheaded by innovative programs such as SNUPPS-has paid off.
----------
Will Davis and ANS acknowledge the help of Glenn Williams in providing support for this article by way of information and critique. Also consulted were the following issues of Nuclear Engineering International magazine: November 1975, September 1977, July 1985.
Note: There was another project in the United States other than SNUPPS to build perfectly identical nuclear plants at multiple locations simultaneously. This was Duke Power's "Project 81," which would have seen three units built at the Cherokee site, and three units at the Perkins site (all cancelled.) This project was all for one utility and was all "in house" as Duke Power designed and built its own power plants. The verification of the duplication concept, however, is significant.
The two completed SNUPPS units have performed with excellence. See their impressive performance records at the following links: Wolf Creek milestones Callaway milestones
________________________________________________________
Will Davis is Communications Director, historian, newsletter editor and board member for the N/S Savannah Association, Inc. He is a consultant to the Global America Business Institute, a contributing author for Fuel Cycle Week, and writes his own popular blog Atomic Power Review. Davis is also a consultant and writer for the American Nuclear Society, and serves on the ANS Communications Committee. He is a former US Navy reactor operator, qualified on S8G and S5W plants.