Marviken–The world’s only oil-fired nuclear power plant
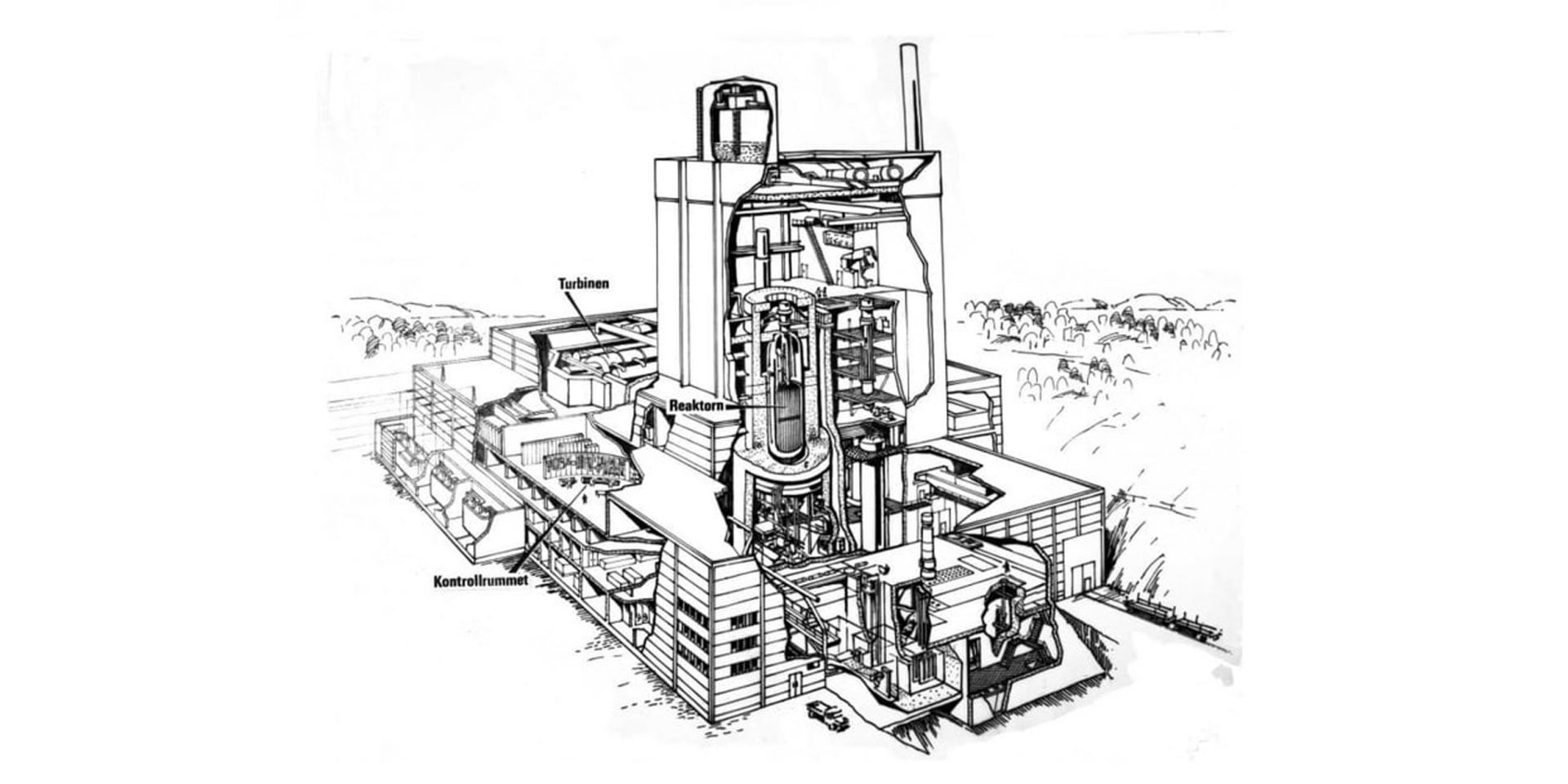
In the late 1950s, the Swedish government decided to undertake a large-scale nuclear energy project. Situated about 75 miles southwest of Stockholm on the Baltic coast, Marviken was located on a peninsula, allowing for the cooling water intake and outlet to be located on either side of the peninsula. The coastal location also allowed the large reactor pressure vessel to be delivered by ship.
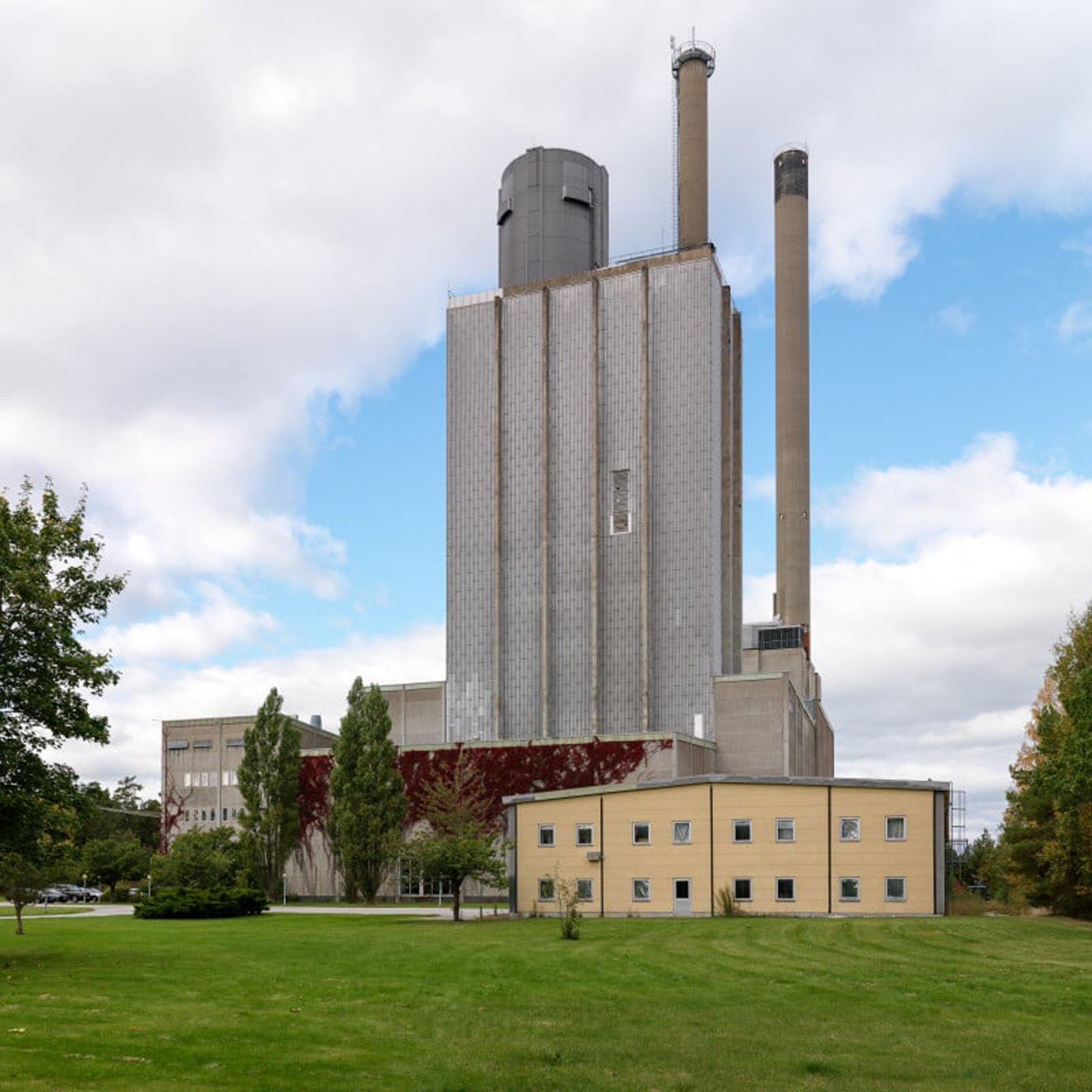
The Marviken nuclear power plant. (Photo: Vattenfall)
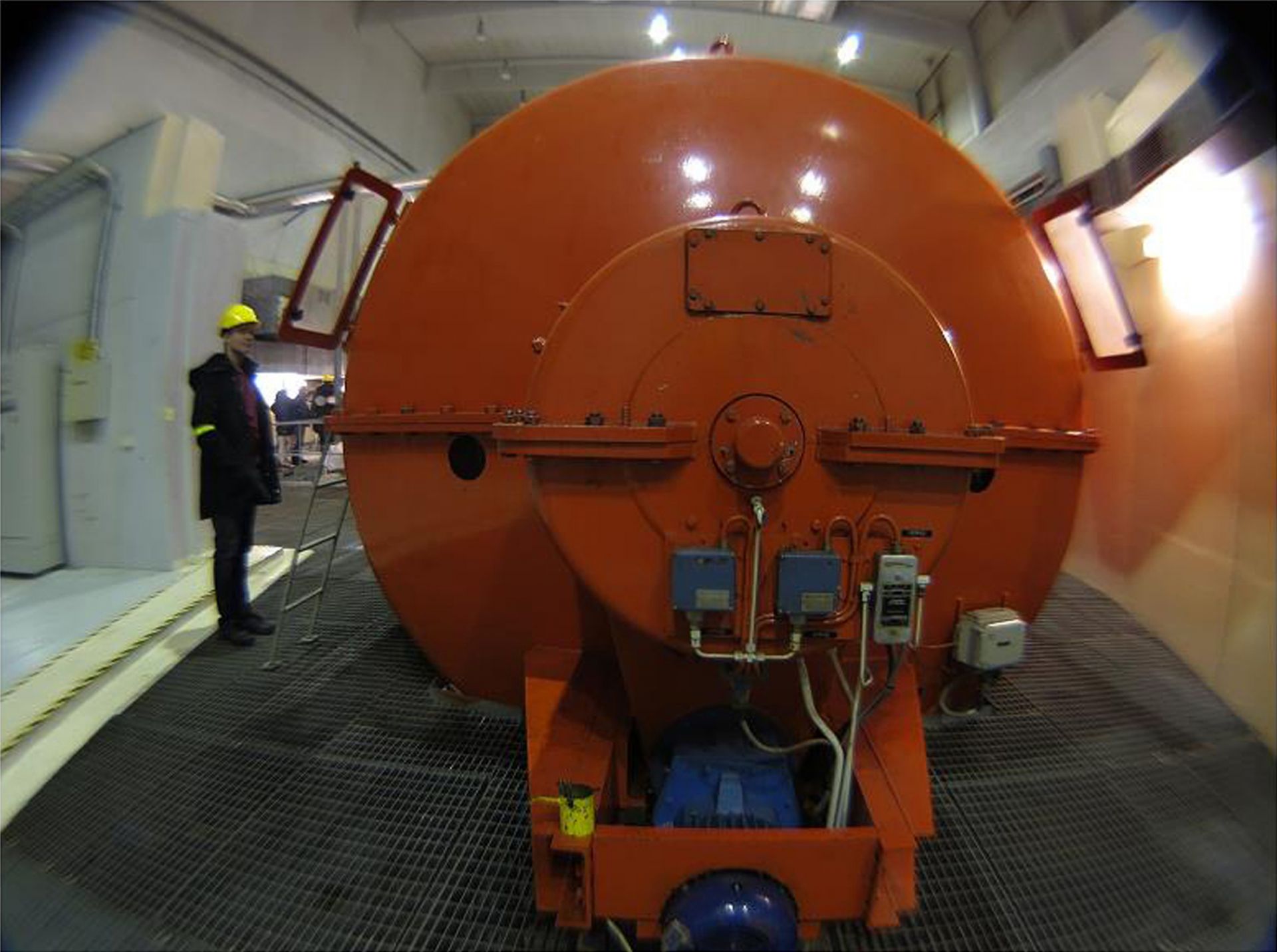
The turbine. (Photo: Jitka Zakova/Nuclear Power? Yes Please)
Marviken was a direct-cycle boiling heavy water reactor that was both moderated and cooled by heavy water. The relatively small reactor was to use slightly enriched uranium. One of the design goals was for Marviken to eventually be able to superheat steam, increasing the turbine output. Design output for the reactor was 140 MWe with saturated steam, or 200 MWe utilizing superheated steam.
Site preparation construction began in November 1963. The reactor was to be built by the Swedish State Power Board and AB Atomenergi. In 1964 the Swedish company ASEA was chosen as the main contractor, and construction of the reactor building began in 1965. By 1968, testing of reactor systems had begun. Functional testing involving the reactor and turbine was performed in 1969.
The reactor contained 36 fuel rods. To control the reactor, there were 24 safety rods and 16 regulating rods. The safety rods could be actuated quickly to shut down the reactor, while the regulating rods could fine-tune reactor power levels during operation. Marviken was designed to be subcritical at operating temperatures with all regulating rods inserted into the core. To reach criticality, the regulating rods would be extracted from the core in a specified sequence. It could reach a critical state with only a few of the regulating rods withdrawn. There was also a boron injection system in the event of safety rod failure.
Marviken was designed to be controlled manually at low power levels by operators manipulating the regulating rods. To maintain a set reactor output, a system was engineered to compare the actual reactor power level to the power level manually set by reactor operators. This system would automatically step regulating rods in or out until there was alignment of the actual reactor output and operator-set output.
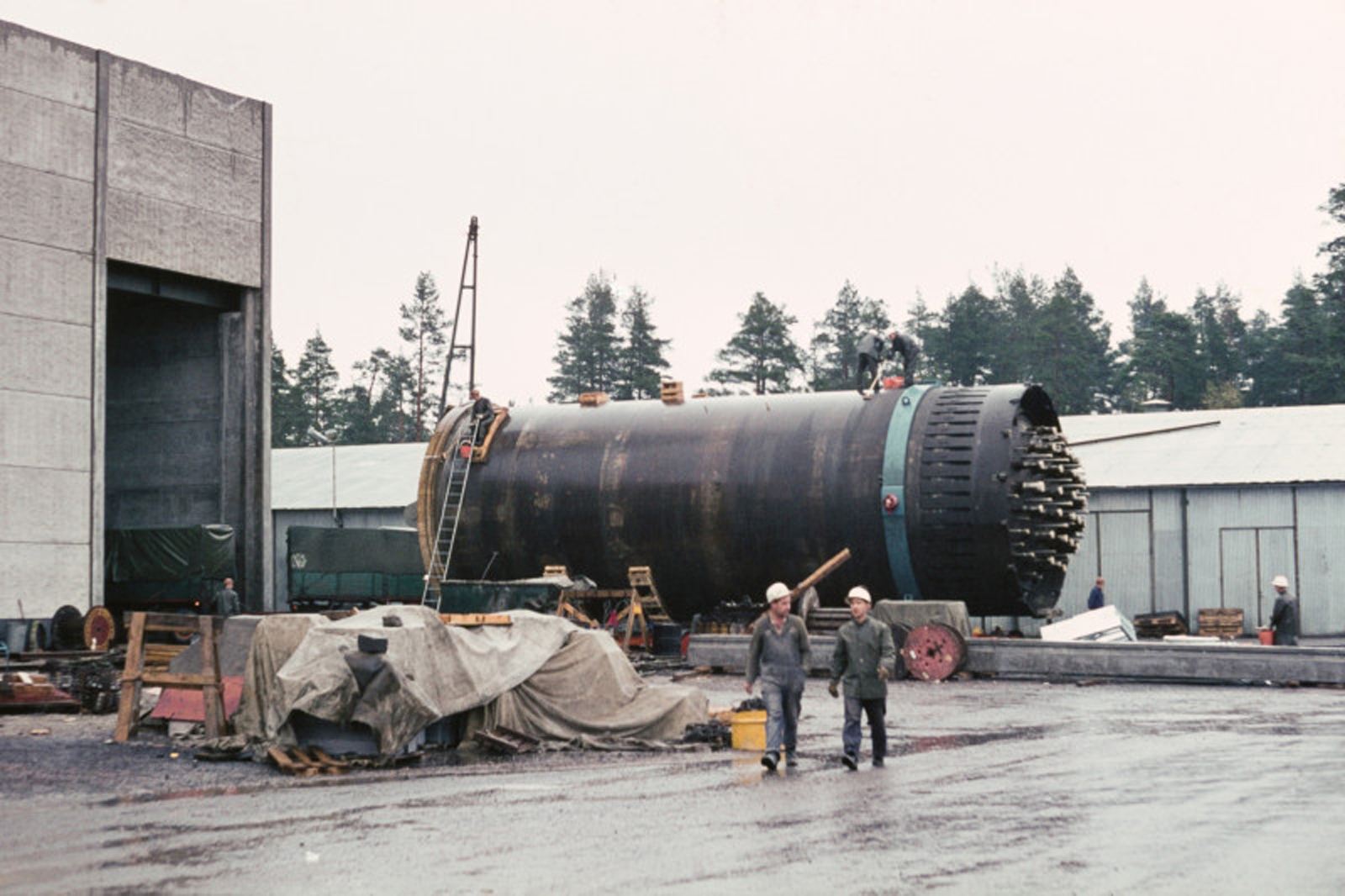
The lower half of the reactor tank on its way to the reactor building. (Photo: Vattenfall)
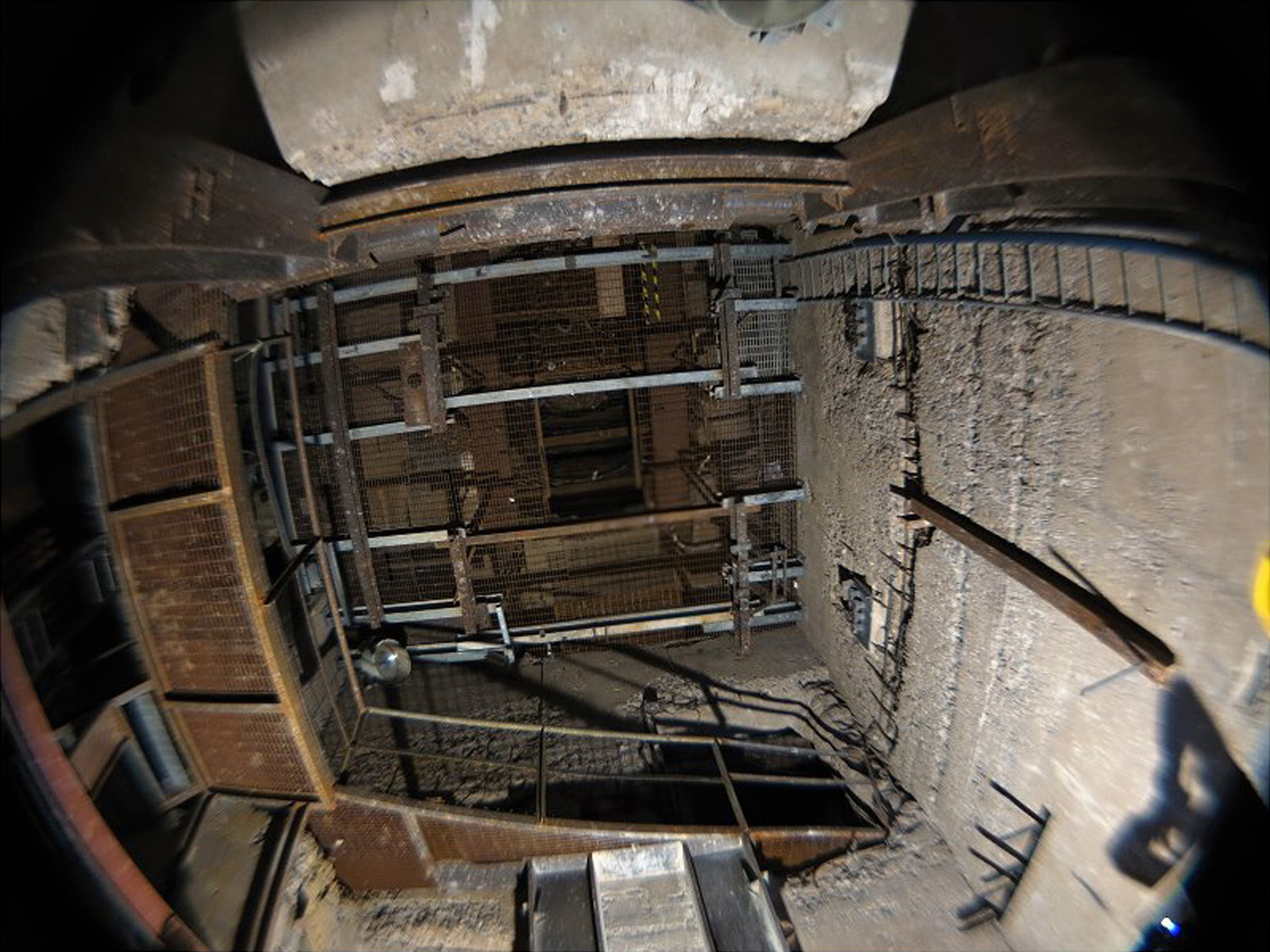
Inside the drywell, the bottom of the reactor vessel is hinted at near the top of the picture. (Photo: Jitka Zakova/Nuclear Power? Yes Please)
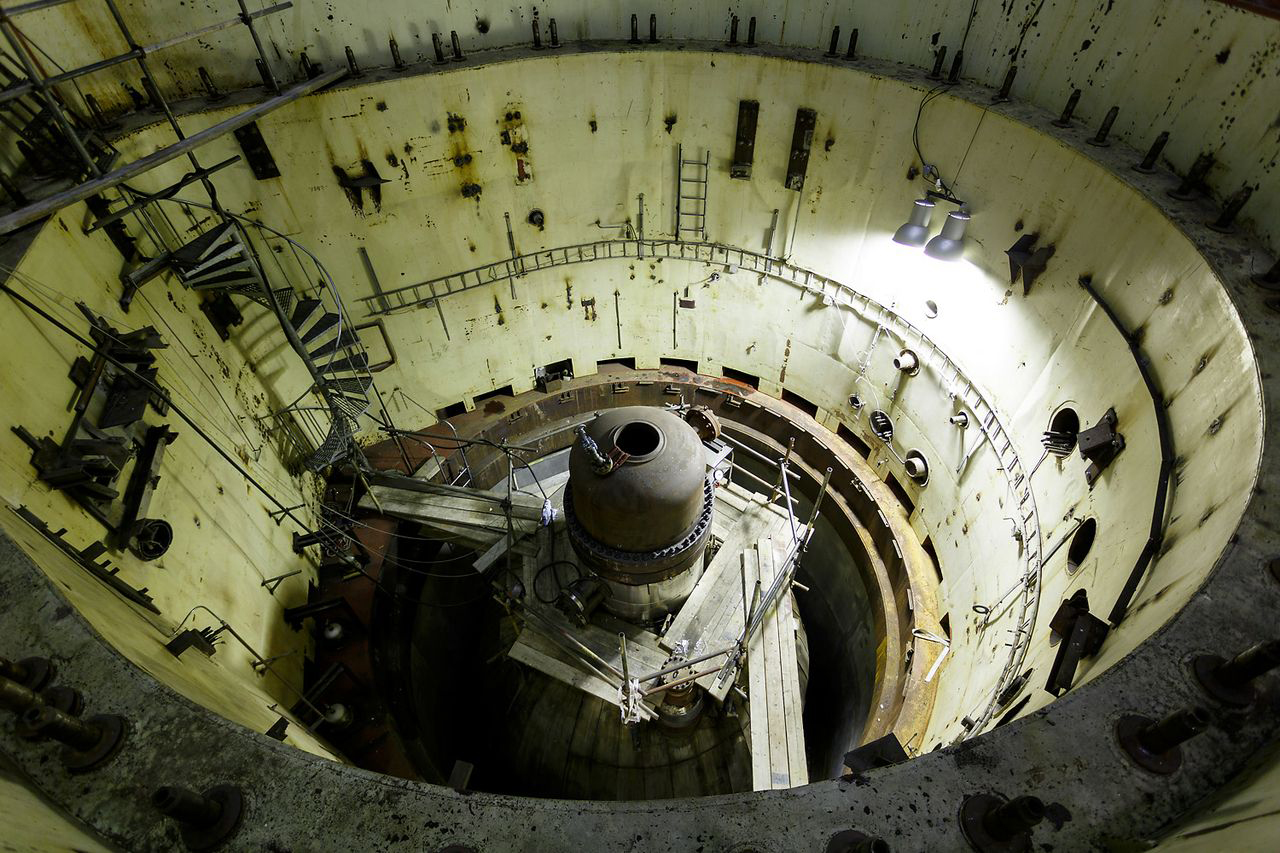
The reactor tank within the containment. (Photo: Jitka Zakova/Nuclear Power? Yes Please)
The turbine was rated at 200 MWe and was designed to run on superheated steam. It was anticipated that during the first few years of operation the turbine would operate on saturated steam until plans for using the superheater section of the reactor were finalized. Producing 200 MWe could be accomplished by using superheated steam at a pressure of 594 psi and temperature of 475°C (887°F). The turbine was in a shielded building due to radiation concerns. Remote operation of the turbine was necessary, as was remote monitoring equipment. Turbine throttle operation could be controlled by a servo system to maintain reactor pressure at a desired level, and access to the turbine during operation was not allowed.
Although the reactor was never loaded with fuel, hot water testing was carried out with light water, during which a few issues were noted. Steam was condensing in the superheater channels that under certain conditions could lead to more moisture in the turbine than was originally planned for. There were also issues with improper functioning of the electrical control rod indication system. The reactor temperature regulating system could not be tested properly, because the large circulating pump failed early on due to insufficient lubrication in the pump support bearing.
These issues were to be worked out prior to fuel loading. However, despite the planning, construction, and initial testing, Marviken was never officially loaded with fuel. The combination of issues discovered during testing combined with the Treaty on the Non-proliferation of Nuclear Weapons that Sweden ratified in 1968 prevented further progress in starting up the plant. According to the World Nuclear Association, “The project was mired with technical and design problems stemming from the dual requirements for the reactor to produce both electricity and plutonium for the Swedish nuclear weapons program. The reactor was never loaded with fuel and was decommissioned in 1970.”
Shortly after, an oil-fired steam boiler was added to the plant to heat steam. Using the turbine built for Marviken, it produced electricity for the Swedish electrical grid during times of peak loading. As time went on, Sweden built more advanced nuclear energy generation capability, and Marviken was retired in 2009.
Marviken further served the nuclear industry as the site of an important set of tests carried out that supported BWR reactor technology. The Nuclear Energy Agency detailed series of experiments that were conducted, including the following.
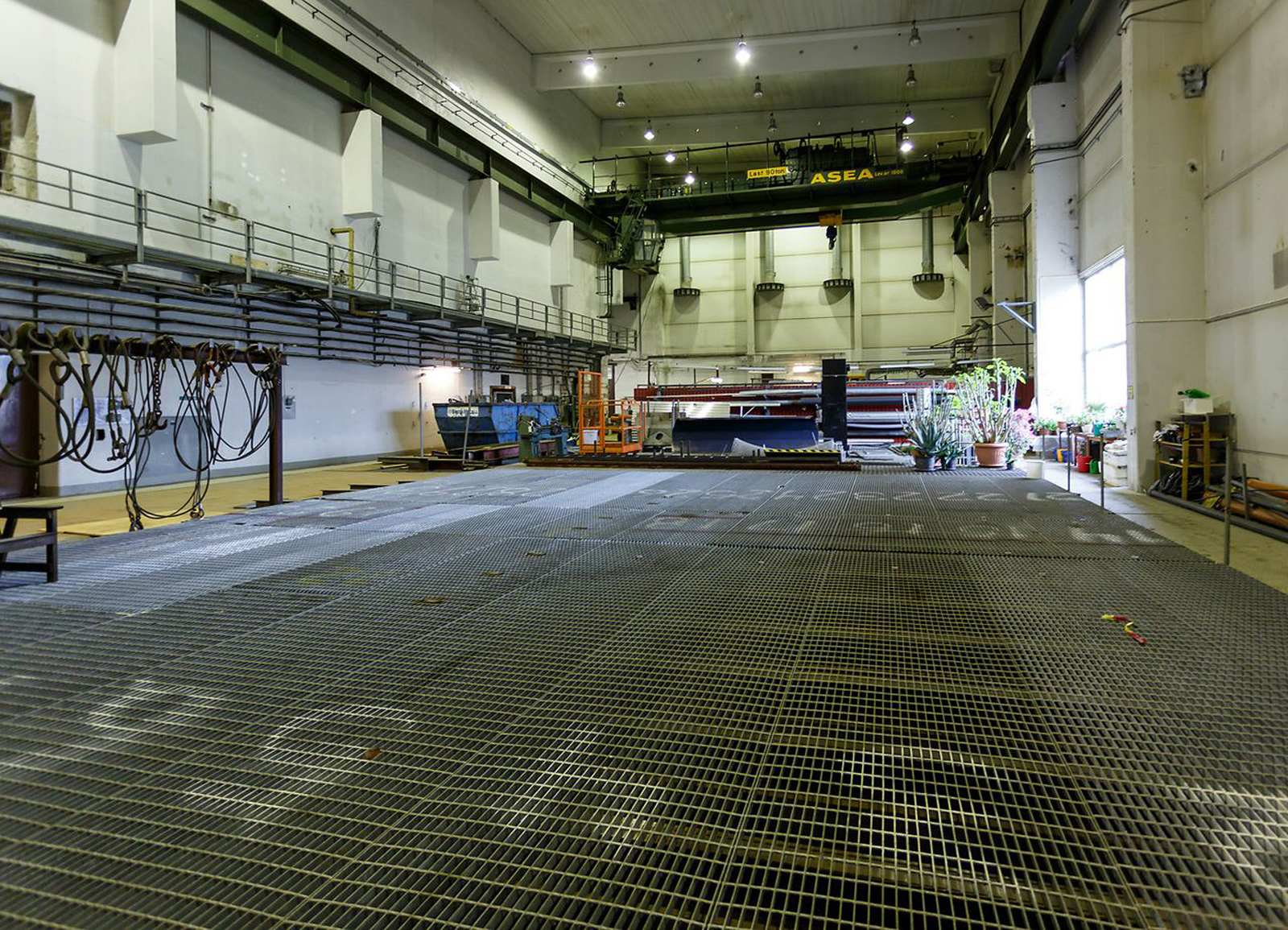
On top of the fuel pool. (Photo: Jitka Zakova/Nuclear Power? Yes Please)
MARVIKEN Full-Scale Containment Blowdown Experiments, Series I
(FSCB-I)
A series of full-scale reactor containment experiments was performed in the Marviken Power Station, the abandoned Swedish nuclear plant, which was originally built as a direct cycle BHWR with natural circulation. These experiments were oriented toward the enhancement of reactor safety and were carried out as a joint project. The experiments included studies of:
containment response to simulated ruptures in pipe systems connected to the pressure vessel—blowdown
iodine transport within the containment and containment leakage during and after blowdown
auxiliary component response to and behavior under loss of coolant accident conditions within a containment.

Diagram of the Marviken reactor vessel. (Image: Vattenfall)
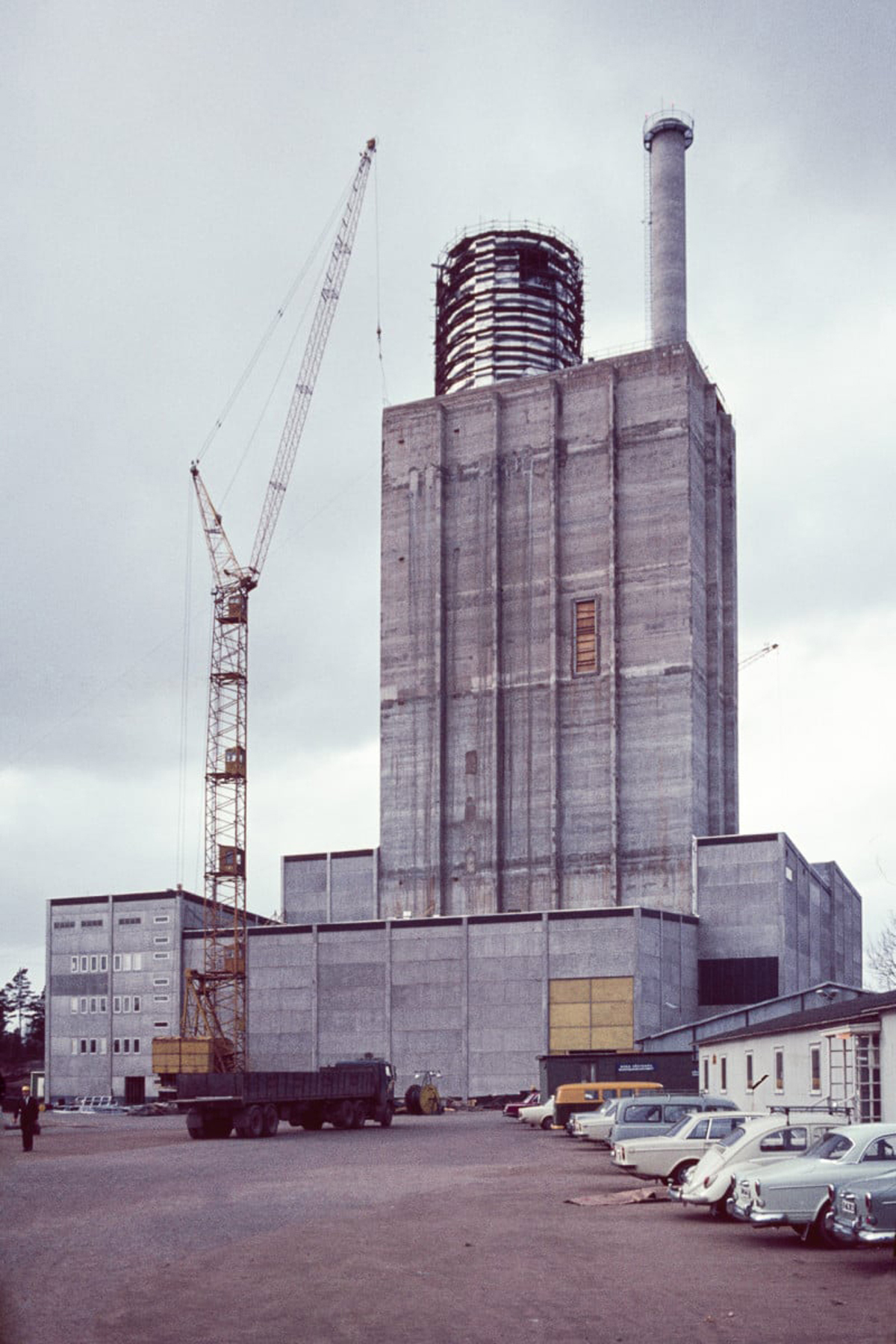
The reactor building under construction. (Photo: Vattenfall)
MARVIKEN FSCB-II
A second series of nine full-scale containment response tests to blowdown was carried out at Marviken, Sweden, in 1976. These new experiments were supplementary to the first series of sixteen tests and were mainly oriented toward studies of oscillatory phenomena inside the containment. Specifically, the objective was to provide information on pressure oscillations in the vent system and in the wetwell water pool under different conditions. The measurement system had been significantly augmented as compared with that of the previous test series and allowed the oscillations to be studied for frequencies up to 100 Hz. These experiments were carried out as a multinational project, as in the first series of tests.
MARVIKEN Full Scale Critical Flow Tests
The Marviken Full Scale Critical Flow Tests (CFT) were conducted between mid-1977 and December 1979 as a multinational project at the Marviken Power Station.
MARVIKEN Full-Scale Jet Impingement Tests
The Jet Impingement Tests (JIT) project at Marviken constitutes the fourth large-scale reactor safety experiment conducted at the Marviken Power Station and is referred to as the Marviken-IV-JIT project. It was established in March 1980. The testing started in September 1980 and continued for about one year.
MARVIKEN Aerosol Transport Tests
The fifth International Reactor Safety Research Project conducted at Marviken, Sweden, comprised a series of Aerosol Transport Tests (ATT) that were performed between 1983 and 1985. A total of five tests were performed. The ATT project studied on [a] large scale the effects of low-probability severe accidents in water-cooled reactors leading to overheated core materials. Such postulated accidents were represented by the vaporization of fission product simulants with or without reactor core simulants in the presence of steam, nitrogen, argon, and hydrogen. Measurements were made of the thermal hydraulic conditions present in the system, and extensive sampling was undertaken to provide data on aerosol mass concentration and particle size distribution, to identify gaseous species and to obtain a mass balance for the system.
Marviken’s reactor may have never been loaded with fuel, but converting the plant to burn oil ensured that the project still provided some support to the Swedish electrical grid. And perhaps more importantly, the reactor went on to serve the nation of Sweden and the world with functional testing of boiling water reactor safety systems. This information ensured BWRs around the world could be designed and operated safely.
Today, the site is being reenvisioned as the Marviken Smart Energy Cluster, with plans that include incorporating small modular reactors, along with considering thorium reactors that enable the reuse of used nuclear fuel.
Jeremy Hampshire is an ANS member whose avocation is writing about the history of nuclear science and technology. His experience includes time as a lead nuclear quality assurance auditor and a senior nuclear technical advisor.