Hanford runs tests for melter replacements
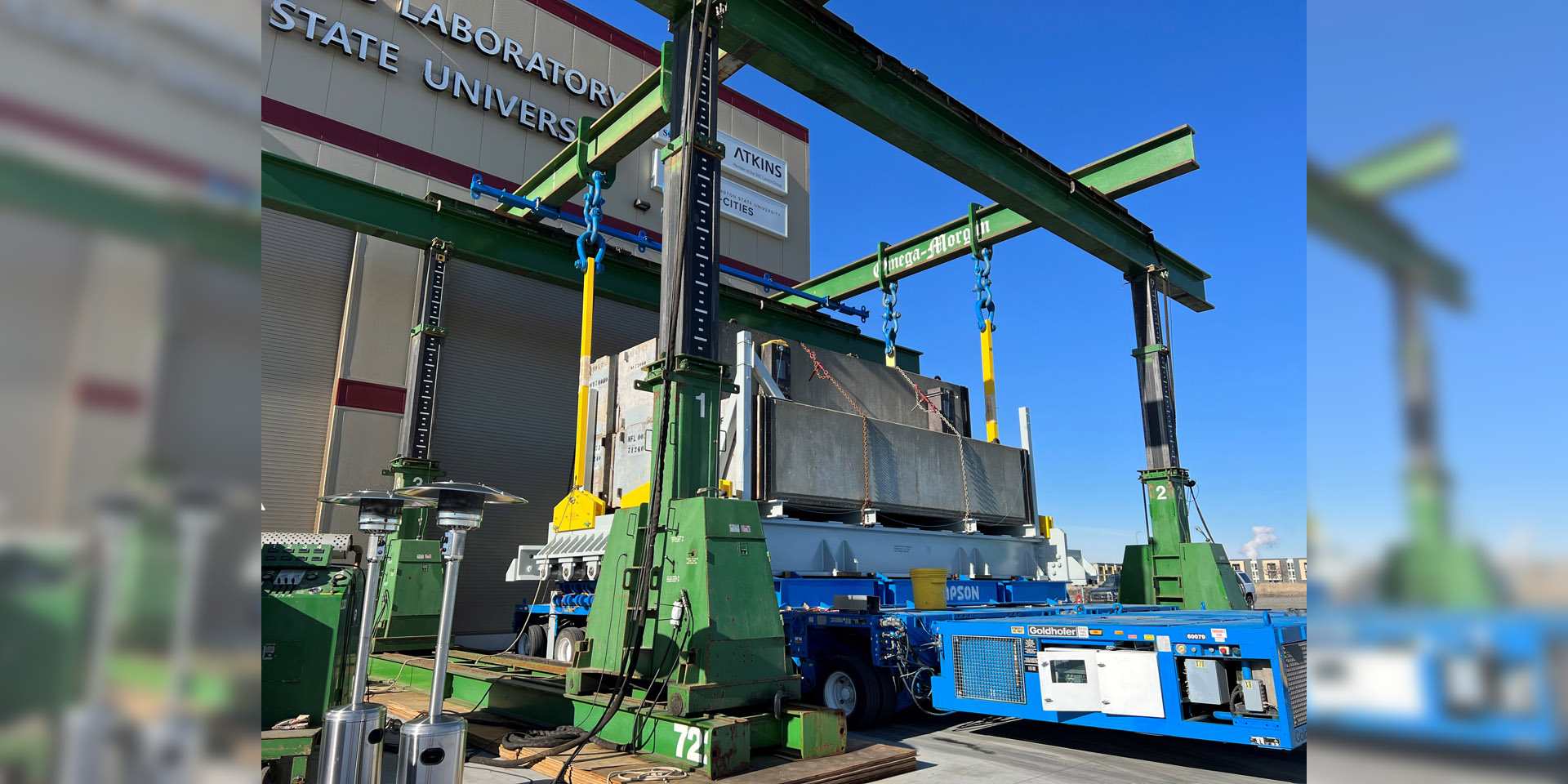
The Department of Energy has announced that tank operations contractor Washington River Protection Solutions (WRPS) and subcontractor Atkins are making progress at the Hanford Site in Washington state in their preparations to provide replacement melters to treat radioactive and chemical tank waste for the site’s Direct-Feed Low-Activity Waste program.