First ITER central solenoid module ready for transatlantic journey
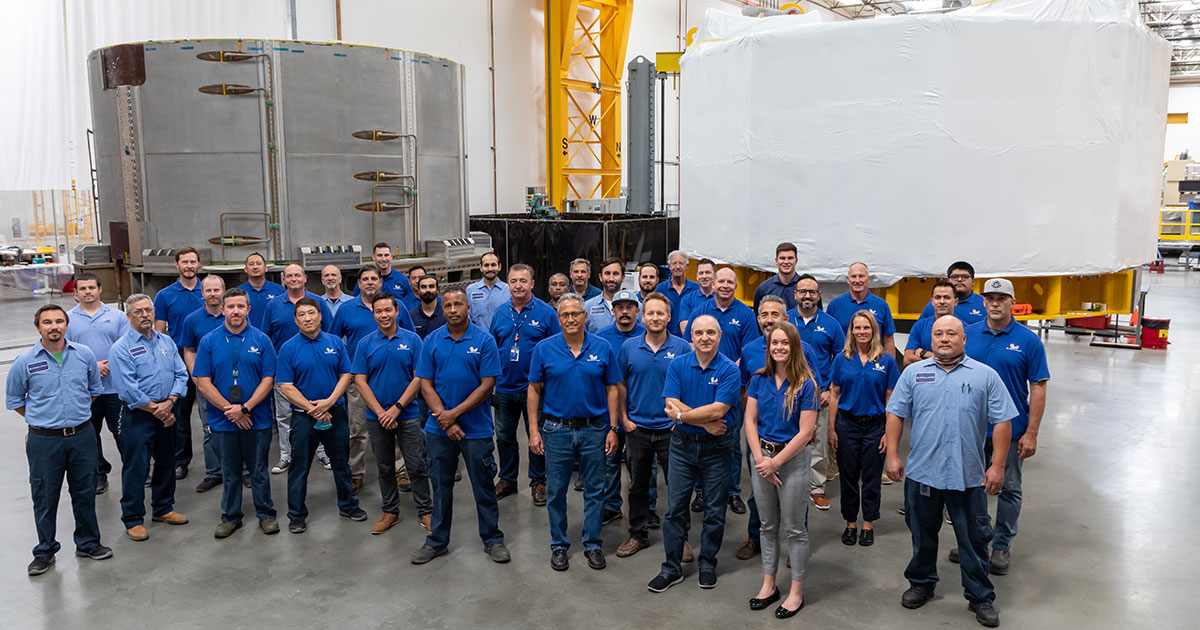
After a decade of design and fabrication, General Atomics (GA) is preparing to ship the first module of the central solenoid—the largest of ITER’s magnets—to the site in southern France where 35 partner countries are collaborating to build the world’s largest tokamak and the first fusion device to produce net energy.