Beyond conventional boundaries: Innovative construction technologies pave the way for advanced reactor deployment
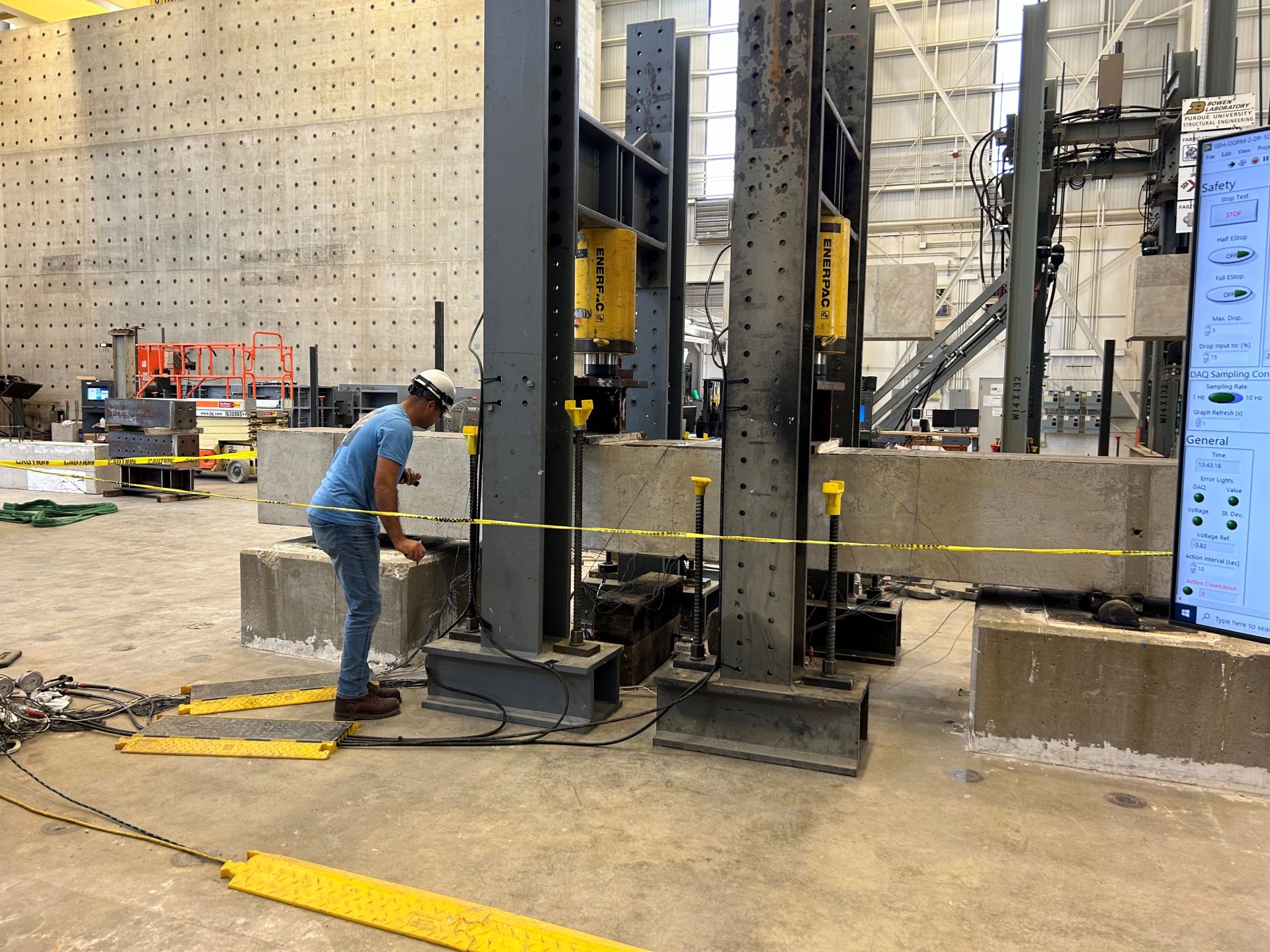
In a bid to tackle the primary obstacle in nuclear deployment—construction costs—those in industry and government are moving away from traditional methods and embracing innovative construction technologies.
Spearheaded by the National Reactor Innovation Center (NRIC) and its industry partners, this new approach is seeking to deploy small modular reactors more efficiently and economically, mitigating cost overruns and scheduling conflicts that typically hinder such projects—and has met with some success.
A development team led by GE Hitachi Nuclear Energy successfully tested a modular steel-concrete composite, one of three advanced construction technologies being explored under the Department of Energy’s Advanced Construction Technology Initiative (ACTI) to reduce nuclear construction costs by 10 percent.
“The major cost of nuclear energy is construction,” said Luke Voss, an Idaho National Laboratory technical program manager for advanced construction. “The industry is seeking better, faster, and more efficient ways to deploy. The ACTI program leverages promising developments from other industries that have not been tested within the nuclear context.”
This DOE-funded project is managed through the NRIC, which was established in 2019 to enable advanced reactor demonstration and deployment. The project was broken into two phases: an initial phase focused on design, testing, and preparing for a demonstration of various construction technologies; and a second phase involving constructing a portion of a full-scale nuclear reactor building to implement these construction technologies and validate various aspects of the process.
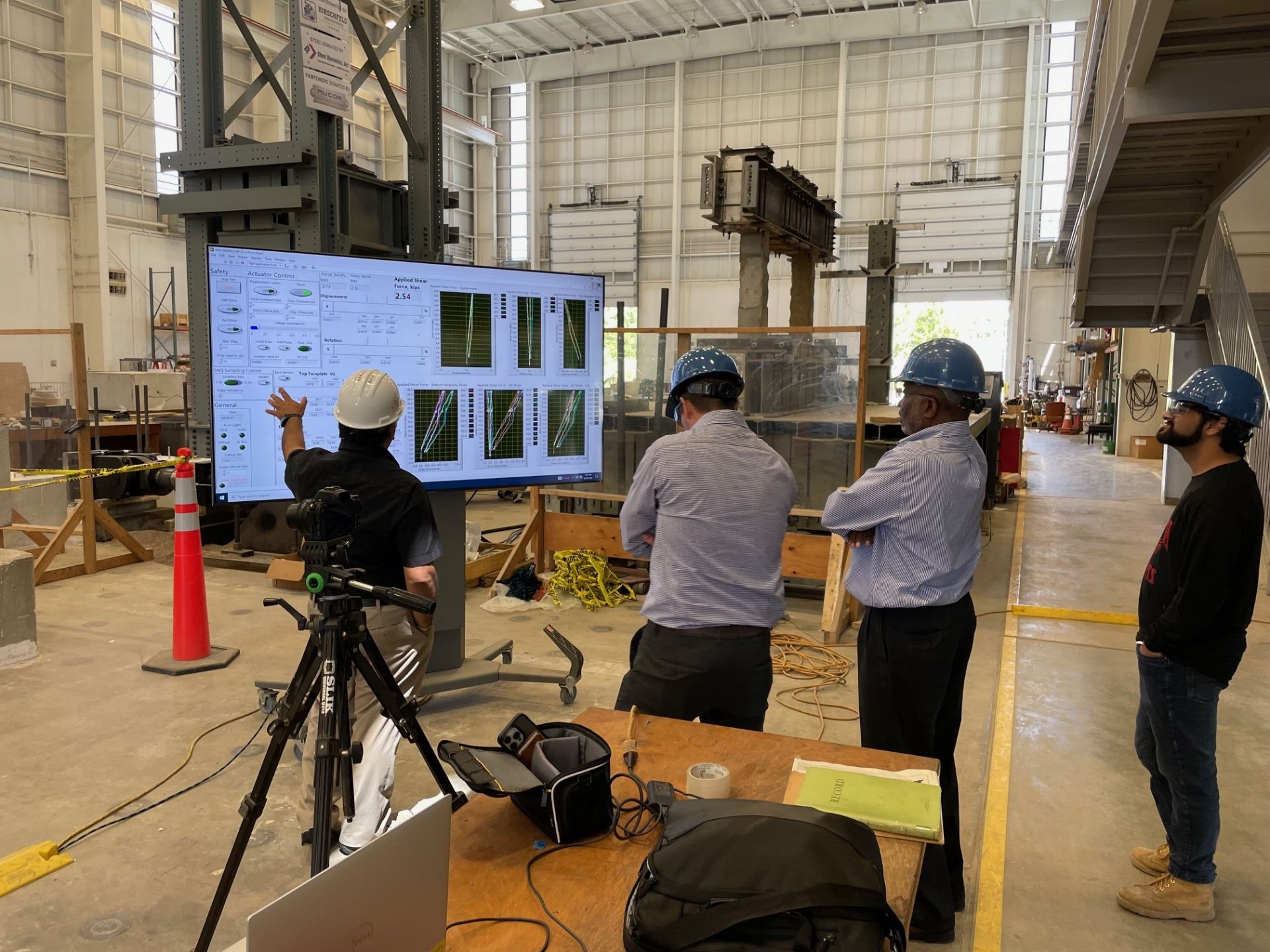
NRIC and NRC members receive an explanation from Dr. Amit Varma about the test specimen performance. (Photo: Purdue University)
The key technology for this project is a modular, steel-concrete composite construction technique called diaphragm plate steel composite (DPSC).
Researchers recently tested DPSC specimens at Purdue University’s Bowen Laboratory in Lafayette, Ind. They filled modular plates with concrete to simulate a reactor containment wall then tested this model by applying different forces, like those experienced during an earthquake, to see how it would hold up. The tests showed that this advanced construction method could be used to build safe and more efficient nuclear reactors.
GE Hitachi hopes to use this DPSC technique for its first SMR project at the Darlington site in Ontario, Canada.
“The successful design, fabrication, and testing of DPSC modules demonstrate the potential of this advanced fabrication and construction technology to lead to cost savings and improved project schedules in the deployment of small modular reactors,” said Sean Sexstone, executive vice president for advanced nuclear at GE Hitachi.
NRIC director Brad Tomer described this as groundbreaking work for the advanced nuclear industry. “NRIC’s model of partnering with industry to develop and test advanced technologies is paving the way for these advanced reactors to become a cornerstone of the future energy landscape,” he said.
Old method, new technique
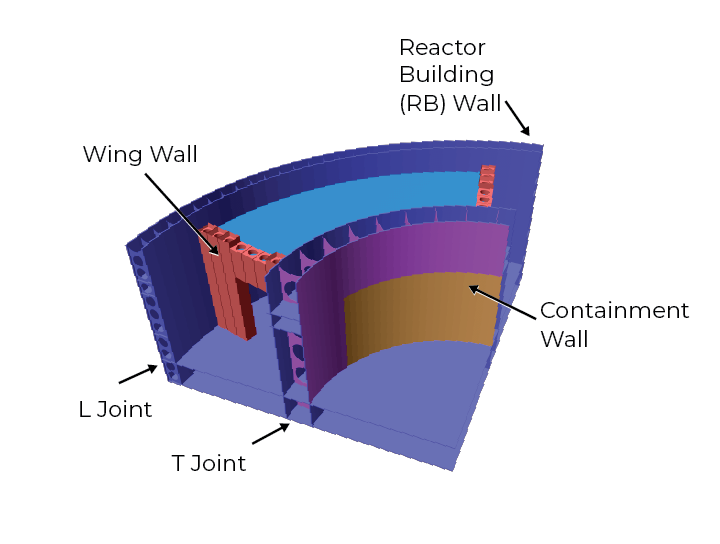
Digital representation of the minimum viable product for a reactor building demonstration. (Image: INL)
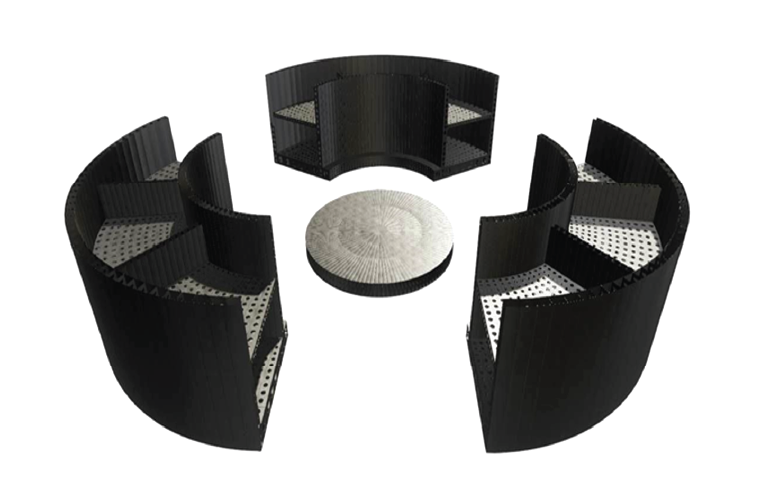
Steel-concrete composite wall sections fabricated in-shop and shipped to site for final assembly. (Image: INL)
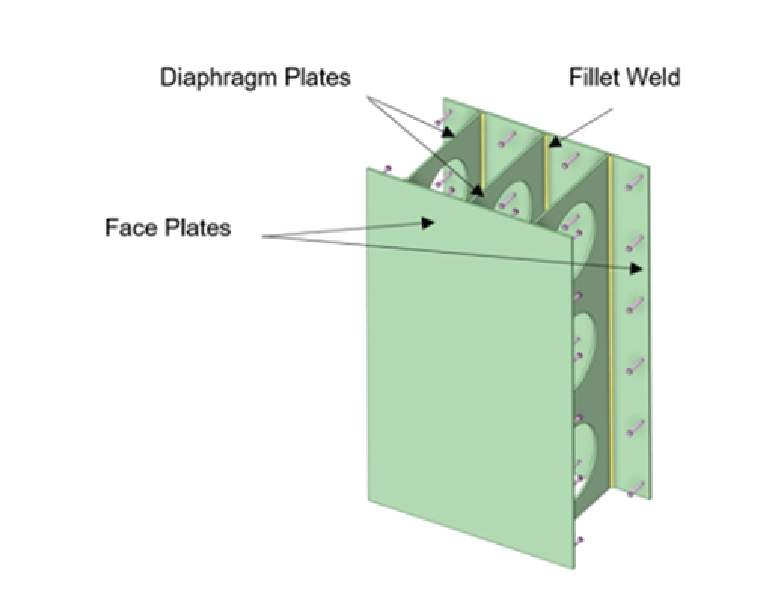
Diaphragm plate steel composite. (Image: INL)
The DPSC technique is not new in the construction industry, but it is now being applied in nuclear reactor construction. It has several benefits over traditional methods for building with steel and concrete. It uses large, continuous steel plates connected by metal pieces with holes, called diaphragms, that let concrete flow through, making the structure strong and safe.
The steel wall modules are fabricated in a controlled factory setting, improving the quality of welding and inspection, compared with traditional on-site construction. This approach also allows walls to be constructed in parallel with site preparation instead of the sequential methods of the past. In addition, DPSC eliminates the need for rebar, which significantly reduces site work. The steel wall sections are shipped to the site and welded together to create a full containment system. The completed steel containment system is then filled with concrete on-site. This significantly reduces site work, saving on labor costs and project time.
These modules can also be customized with different materials on each side of the wall to handle specific needs, like preventing corrosion in nuclear power plants. During installation, the modules can be welded together end-to-end or stacked on top of each other, allowing for flexible designs and quicker quality checks.
By replacing traditional forms—temporary structures or molds used to shape poured concrete until it hardens within a reinforced framework—DPSC streamlines the construction process.
SMRs face challenges related to economies of scale, compared with larger reactors. Because SMRs produce less electricity (typically in the range of megawatts) than large reactors (which produce gigawatts), the cost per kilowatt of electricity generated can be higher. Making electricity production as cost-effective as possible is crucial for the competitiveness and viability of SMRs.
“This is a significant milestone for the future of small modular reactors,” Voss said. “The design is practical, and the test results have been very encouraging.”
Next steps
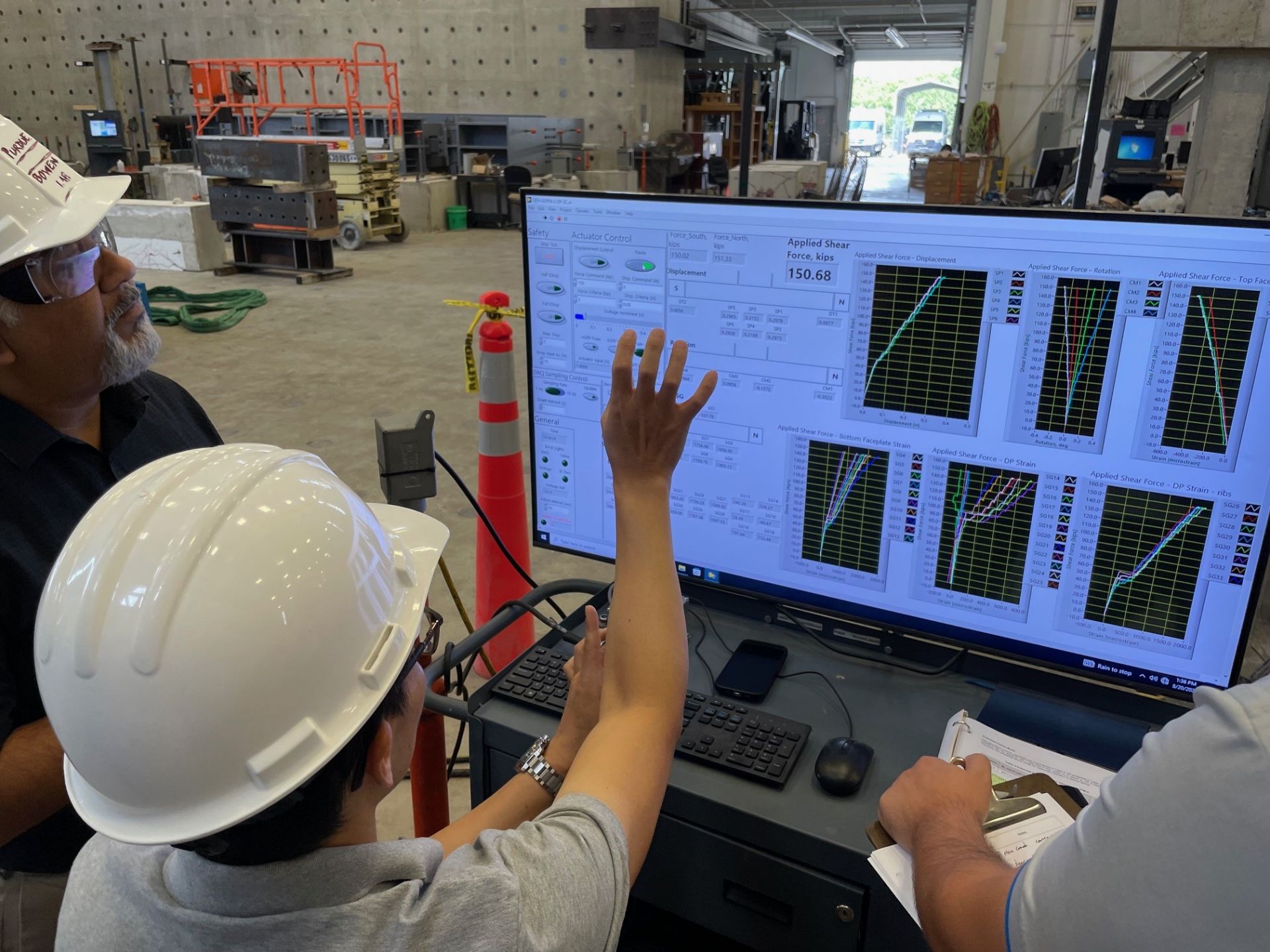
Members of the Purdue University team interpret the stress/strain digital readout of the test specimen. (Photo: Purdue University)
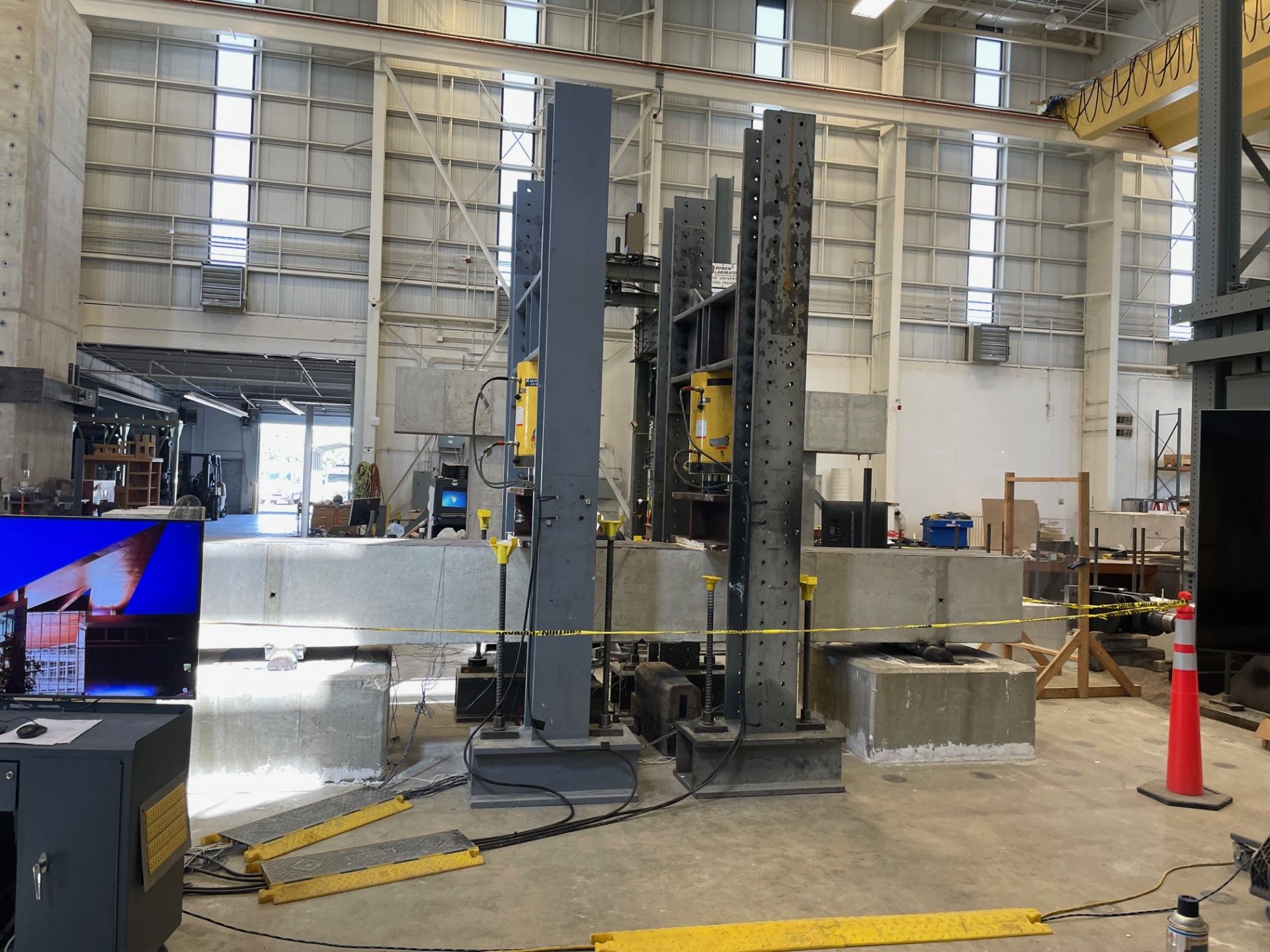
A DPSC test specimen in a two-point load test. (Photo: Purdue University)
The next phase focuses on constructing a portion of an actual reactor building to offer insights that can improve efficiency and reduce cost. That phase will also build confidence among stakeholders and investors that the technology is ready for commercial deployment.
The NRIC is evaluating a proposal from GE Hitachi to build a portion of a reactor containment building using DPSC for the walling system to test the technology. If approved by the DOE’s Office of Nuclear Energy, construction could start this summer and be completed next year.
The demonstration will use digital twin technologies, which create a virtual model of the reactor, and nondestructive evaluation techniques developed in the first phase of the project. “These technologies help us monitor and inspect the structure without causing any damage,” Voss said.
The NRIC plans to show several technologies that could significantly lower the cost of building containment facilities for new nuclear reactors and reduce the risks and uncertainties associated with the construction schedule.
“Our advanced construction program follows the principle, ‘we learn by doing,’ focusing on demonstrating and learning in real-world scenarios to quickly inform the industry,” said Voss. “Overall, this development is poised to bring significant benefits to the industry, and that’s something we’re really enthusiastic about.”
Donna Kemp Spangler is a senior communications strategist at Idaho National Laboratory.