Fukushima Daiichi: 10 years on
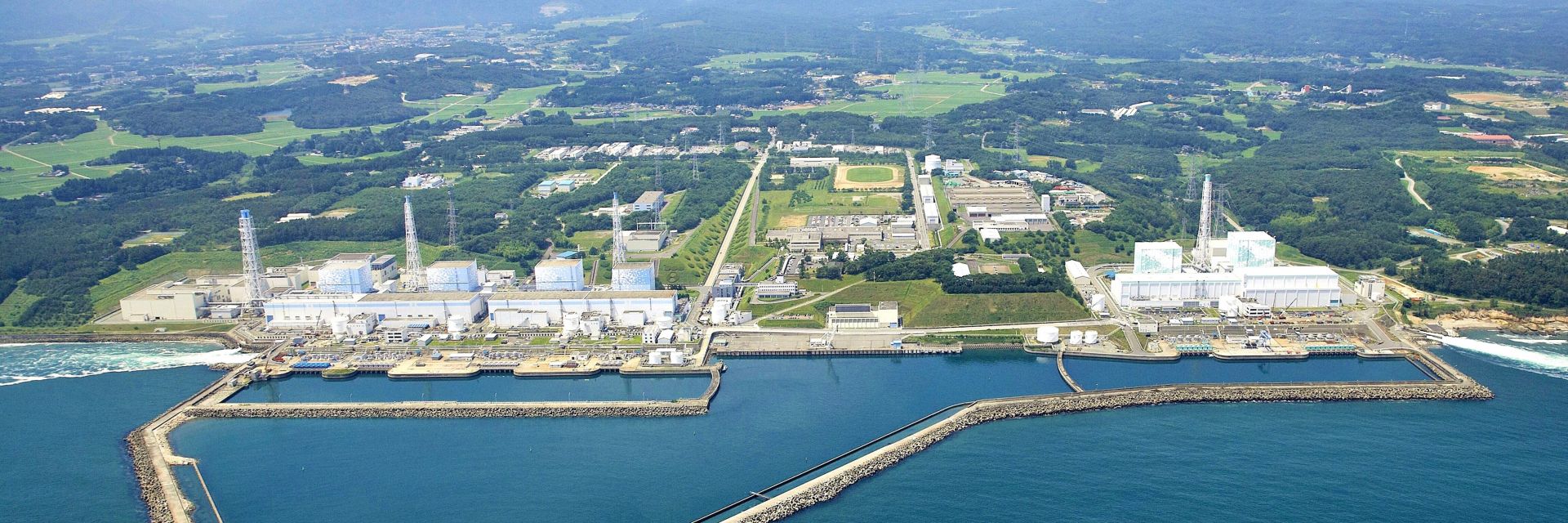
The Fukushima Daiichi site before the accident. All images are provided courtesy of TEPCO unless noted otherwise.
It was a rather normal day back on March 11, 2011, at the Fukushima Daiichi nuclear plant before 2:45 p.m. That was the time when the Great Tohoku Earthquake struck, followed by a massive tsunami that caused three reactor meltdowns and forever changed the nuclear power industry in Japan and worldwide. Now, 10 years later, much has been learned and done to improve nuclear safety, and despite many challenges, significant progress is being made to decontaminate and defuel the extensively damaged Fukushima Daiichi reactor site. This is a summary of what happened, progress to date, current situation, and the outlook for the future there.